<!—->
<!– –>
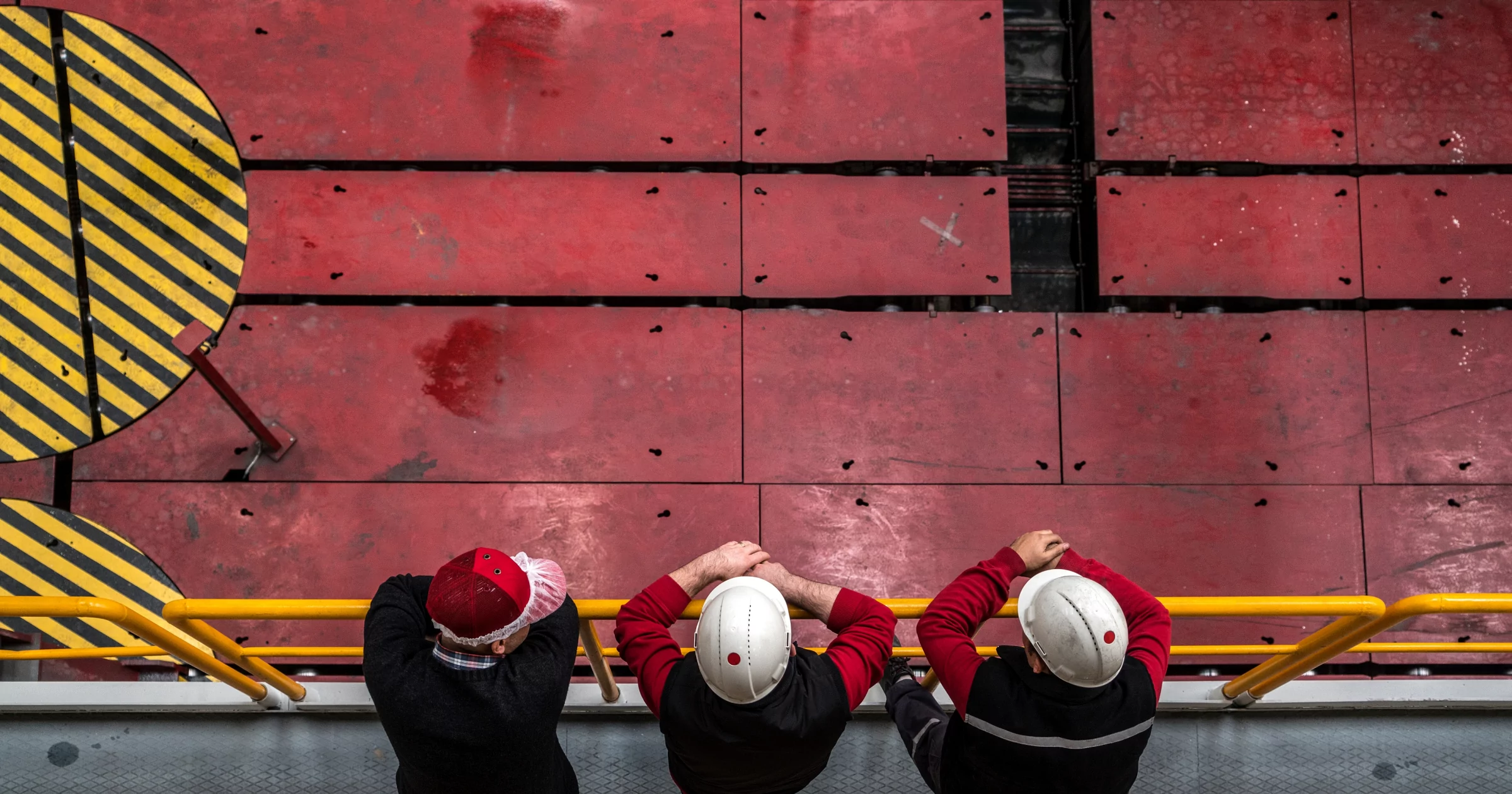
Reshoring manufacturing to the US has been a significant trend in recent years, driven by geopolitical tensions, supply chain disruptions, proximity to customers and markets, eco-system synergies and the need for positive impact on the domestic economy. However, reshoring presents several challenges—mainly workforce, technical and economic issues.
AI, automation and digital labor can help tackle these challenges. For organizations willing to take these challenges head on and become Transformational Optimizers from the start, this is also an opportunity to skip ahead generations of manufacturing evolution and adopt technologies that will help outperform competition from the start.
Here are some concrete recommendations and examples from IBM for companies considering reshoring manufacturing:
Workforce challenges
One of the primary obstacles to reshoring is accessing a skilled manufacturing workforce. According to a report by the Manufacturing Institute, 5 out of 10 open positions for skilled workers in the US manufacturing industry remain unoccupied today due to the skills gap crisis. Reshoring production requires workers with technical skills to operate computer-controlled equipment as well as soft skills like problem-solving.
To address this challenge, companies can use digital labor to supplement the existing workforce by automating repetitive, dangerous or complex tasks. For example, collaborative robots (cobots) can work alongside human workers to perform tasks that require precision or dexterity, freeing up human workers to focus on higher-value tasks. Additionally, AI-powered tools can help identify skills gaps and provide personalized training programs to cross-skill employees.
According to studies quoted by Deloitte, it is estimated that AI and machine learning will contribute to a 37% increase in labor productivity by 2025. Moreover, a study by the World Economic Forum found that by 2025, automation and a new division of labour between humans and machines will disrupt 85 million jobs, but they will also create 97 million new roles, highlighting the need for workers to acquire new skills.
Technical challenges
Reshoring production presents process and infrastructure challenges. Manufacturing overseas allowed longer production runs with cheaper changeover costs between products, whereas reshoring requires greater flexibility and agility in production systems.
Digital labor can make processes more adaptable. Digital twin technology creates virtual representations of physical assets to simulate changes, allowing companies to test and optimize production processes before implementation. Machine learning algorithms can continuously optimize operations, improving efficiency and reducing waste.
The total number of service robots sold for professional use hit 158,000 units in 2022—an increase of 48% according to a report by the International Federation of Robotics. Implementing these technologies requires upfront investment but results in more efficient, cost-effective production overall. This can help US manufacturers catch up in critical EV components like batteries, where Chinese firms currently lead.
Economic challenges
While reshoring removes supply chain risks of overseas production, the economics must still make sense. Boston Consulting Group estimates reshoring will add 10-30% in costs versus offshoring. A report by Forrester found that businesses that implemented automation were able to reduce operational costs by 25-50%. Automating tasks with digital workers also lowers overall labor costs compared to (comparatively) lower wage countries like China.
Companies must balance short-term implementation costs against longer-term savings and strategic benefits. Companies that invest in digital technologies can achieve cost savings and revenue growth. Moreover, a study by the National Bureau of Economic Research found that automation can lead to short-term job displacement but can also lead to long-term job growth.
Case studies
Below, we look at two case studies—the semiconductor industry and EV batter manufacturing—which show how digital labor can help address the challenges of reshoring manufacturing to the US.
Case study 1: Semiconductors
The semiconductor industry provides a pertinent example of reshoring challenges and solutions that could be applied. Semiconductors are essential components for critical industries like computers and communications, but disruptions to their supply chain threaten the global economy.
The current semiconductor supply chain is global and complex, with design, equipment manufacturing, fabrication, and assembly happening in different countries. The US’s share of fabrication has declined from 37% in 1990 to only 12% currently. To meet capacity for critical applications, the US needs to add about 18-20 new semiconductor fabrication plants (“fabs”), requiring 70-90,000 new jobs—a 50% increase over the current workforce. However, many semiconductor manufacturing roles are declining due to automation while engineering roles are rising. This creates a need for upskilling and reskilling of the existing workforce.
Digital technologies can help address the workforce challenges in the semiconductor industry. AI-powered tools can identify skills gaps and provide personalized training programs to cross-skill employees. Digital twin technology can simulate and optimize production processes, reducing the need for physical prototypes and accelerating the development of new products. Collaborative robots can work alongside human workers to perform repetitive tasks, freeing up human workers to focus on higher-value tasks.
Implementing digital technologies requires upfront investment, but it can lead to more efficient, cost-effective production overall. Reshoring semiconductor manufacturing to the U.S. can also reduce supply chain risks, improve proximity to customers and markets and create an ecosystem of suppliers and innovation. It can also help address the skilled workforce gap by creating new job opportunities and upskilling the existing workforce.
In conclusion, the semiconductor industry provides a compelling example of how digital labor can help address the challenges of reshoring manufacturing to the US. By leveraging digital technologies, companies can overcome workforce, technical and economic challenges and achieve strategic benefits.
Case study 2: EV battery manufacturing
EV battery manufacturing in the US presents unique challenges in workforce, technology, and economics. However, as with the previous example of semiconductor manufacturing, these challenges can be addressed through the adoption of AI, automation and digital labour.
The global EV battery supply chain is largely centered in Asia. To meet its ambitious EV goals, the US needs to increase domestic battery manufacturing capacity. This requires significant infrastructure expansion and workforce training. Automation can address workforce challenges by taking over repetitive tasks, freeing up the workforce for more complex tasks. Digital twins can simulate the battery production process, allowing for testing and optimization before actual implementation. Implementing these technologies requires significant upfront investment. However, automation can lead to more efficient, cost-effective production, enabling US manufacturers to compete globally. It can also contribute to reducing battery pack costs, a major component of overall EV costs.
EV battery manufacturing located in the US can also provide strategic benefits. It can secure the supply chain, reduce dependence on foreign suppliers, foster innovation, contribute to job growth, and help bridge the skills gap.
Conclusion
The challenges associated with reshoring manufacturing to the US are addressable: workforce, technical and economic issues can be tackled by the adoption of AI, automation and digital labor. Additionally, this is a once-in-a-lifetime opportunity for manufacturers as they “greenfield” their way back into the US. Consider adopting these foundational traits that set apart the leaders and companies who are reshoring:
- A modern cloud platform. A hybrid cloud IT infrastructure that capitalizes on both public and private cloud solutions lets manufacturers process data where it makes the most sense.
- A robust data foundation. By democratizing big data, organizations can gain deeper insights, drive operational efficiency, and boost cyber resilience.
- Digital technology integration. Cloud platforms can integrate key enabling technologies, such as machine learning, AI, IoT, automation, intelligent workflows, robotics, digital twins, and more.
- New ways of working. Leaders are investing in their workforce, nurturing digital and technology skills to support modern manufacturing solutions.
- Business outcomes linked to cloud. By involving their finance teams, manufacturing front-runners link cloud manufacturing initiatives to quantifiable value.
Download the IBV’s cloud enabled manufacturing report to know more about the five traints that advance your tech-driven priorities.
Are you attending CES, 9-12 Jan, in Las Vegas? Come by the IBM Meeting Center to learn more from our industry experts about the technology that drives the manufacturing industry forward.
More from Automation

December 19, 2023
Anomaly detection in machine learning: Finding outliers for optimization of business functions
5 min read – As organizations collect larger data sets with potential insights into business activity, detecting anomalous data, or outliers in these data sets, is essential in discovering inefficiencies, rare events, the root cause of issues, or opportunities for operational improvements. But what is an anomaly and why is detecting it important? Types of anomalies vary by enterprise and business function. Anomaly detection simply means defining “normal” patterns and metrics—based on business functions and goals—and identifying data points that fall outside of an…

December 18, 2023
Why you shouldn’t use Global Anycast DNS in China
3 min read – Anycast is a standard, table-stakes feature of every authoritative DNS service. It makes sense: inbound queries should always be routed to the best available servers—usually the ones that are geographically closest. Yet, there is one glaring exception: China. The internet in mainland China is walled off from the rest of the world. Any DNS query that crosses into or out of mainland China must pass through a series of filters and other controls before it can be passed along for resolution.…

December 18, 2023
Troubleshoot your network with DNS Insights
4 min read – It is relatively simple to see that something is wrong with your network using DNS data. A spike in NXDOMAIN responses or other errors usually serves as a clear indication that something is amiss. The next step—diagnosing the source of the problem and then actually doing something about those errors—is often a heavier lift. It is a data problem. Any authoritative DNS provider worth its salt will show you how many NXDOMAIN responses you are getting. Yet, few provide the…

December 18, 2023
How to optimize application performance with NS1 traffic steering
2 min read – “I want it now!”—This isn’t just a phrase spoiled children sing; it’s what we demand every time we click a link, stream video content or access an online application. As internet traffic grows in volume and complexity, our expectations for faster response times from the services and content we use rises. We often click away if instant results aren’t provided. For businesses delivering applications and services, the fierce urgency of “now” is a logistical headache. Internet traffic must navigate different…
IBM Newsletters
Get our newsletters and topic updates that deliver the latest thought leadership and insights on emerging trends.
Subscribe now
More newsletters
- SEO Powered Content & PR Distribution. Get Amplified Today.
- PlatoData.Network Vertical Generative Ai. Empower Yourself. Access Here.
- PlatoAiStream. Web3 Intelligence. Knowledge Amplified. Access Here.
- PlatoESG. Carbon, CleanTech, Energy, Environment, Solar, Waste Management. Access Here.
- PlatoHealth. Biotech and Clinical Trials Intelligence. Access Here.
- Source: https://www.ibm.com/blog/reshoring-manufacturing-to-the-us-the-role-of-ai-automation-and-digital-labor/