With technology developing day by day, the way we do business is also changing, and autonomous mobile robots will perhaps be one of the most important business adaptations that the future will offer us.
The accelerated development in artificial intelligence technology, which started at the beginning of last year, has deeply affected many sectors. Many of us now have intelligent assistants whose support we can ask for while doing our work. We can ask them questions, get them to do our work that requires repetition, and often benefit from the alternatives they offer us in the creative process. What about asking an intelligent machine for help with a physical task of ours?
The dream of autonomous mobile robots emerged precisely from this need. This technology, which initially found wide use, especially in the industrial sector, is now used in many sectors such as health, logistics, agriculture and even house cleaning.
Although we may be years away from wide adoption, these mobile robots have the potential to change the way we do business in the future. But how can they manage that? Let us explain.

What are autonomous mobile robots?
Autonomous mobile robots are not your average robots; they are sophisticated machines equipped with advanced sensors, artificial intelligence, and machine learning capabilities. These robots can navigate their surroundings independently, adapting to dynamic environments and responding to real-time changes. Unlike their predecessors, autonomous guided vehicles (AGVs), which rely on predefined paths and are confined to fixed routes, autonomous mobile robots can operate freely, charting their own courses and collaborating with humans to achieve common goals.
The rise of mobile robots is driven by a confluence of factors, including the increasing demand for efficiency, the need for flexibility in manufacturing and logistics, and advancements in robotics and artificial intelligence. These robots are poised to play a pivotal role in shaping the future of work, transforming industries from manufacturing and warehousing to healthcare and retail.
A bridge from the recent past to the future
The concept of autonomous mobile robots (AMRs) has captivated the imaginations of inventors and scientists for decades. The dream of creating intelligent machines capable of navigating their surroundings independently has fueled countless research projects and technological advancements. While the AMRs we envision today are still evolving, their roots can be traced back to the early pioneers of robotics.
The history of AMRs begins with the work of W. Grey Walter, a British neurophysiologist who, in the late 1940s, developed two robots named Elmer and Elsie, also known as Grey Walter’s tortoises. These robots, inspired by biological systems, were designed to exhibit rudimentary autonomous behavior. They could navigate their surroundings using simple sensors and respond to stimuli in an almost lifelike manner.
[embedded content]
Laying the foundation
In the 1960s, the field of robotics took a significant leap forward with the development of Shakey, a mobile robot designed by SRI International. Shakey was equipped with a TV camera, a ranging sonar, and bump sensors, enabling it to perceive its surroundings and make decisions about its movements. While Shakey’s capabilities were limited compared to modern AMRs, it marked a crucial step in the evolution of autonomous mobile robots.
The 1970s and 1980s saw the emergence of automated guided vehicles (AGVs), which were primarily used in manufacturing and warehousing environments. AGVs followed predefined paths, typically marked on the floor with wires or magnetic tape, to transport goods and materials between workstations. While AGVs offered improved efficiency and reduced labor costs, they lacked the adaptability and flexibility of true autonomous robots.
Dawn of autonomous mobile robots
The 1990s and early 2000s witnessed a renewed interest in developing truly autonomous mobile robots. Advancements in sensor technology, artificial intelligence, and machine learning fueled this progress. AMRs were equipped with more sophisticated sensors, allowing them to perceive their surroundings in greater detail and make more informed decisions. Artificial intelligence algorithms enabled AMRs to learn from their experiences and adapt to changing environments.
In recent years, AMRs have gained widespread adoption across various industries, from manufacturing and logistics to healthcare and retail. These robots are revolutionizing material handling, streamlining warehouse operations, automating tasks in healthcare settings, and enhancing customer service in retail environments. AMRs are not just replacing human workers; they are augmenting their capabilities, leading to increased productivity, improved safety, and new possibilities for innovation.
Over time, Grey Walter’s biology-inspired tortoises have evolved into autonomous mobile robots that have reached the ability to do many things in seconds that even humans find difficult to do.
[embedded content]
How do Autonomous mobile robots work?
As we mentioned before, autonomous mobile robots (AMRs) are sophisticated machines that can navigate their surroundings independently, adapting to dynamic environments and responding to real-time changes. They are equipped with a suite of sensors, artificial intelligence, and machine learning capabilities that enable them to perceive, understand, and interact with their surroundings.
Perception
Autonomous mobile robots rely on a variety of sensors to gather information about their surroundings. These sensors include:
- Cameras: Cameras provide AMRs with visual information, allowing them to identify objects, obstacles, and landmarks
- LiDAR: LiDAR (Light Detection and Ranging) sensors use laser beams to measure distances and create 3D maps of the environment
- Sonar: Sonar sensors emit sound waves to detect objects and measure distances
- Bump sensors: Bump sensors detect physical contact with obstacles
- Infrared sensors: Infrared sensors detect heat sources, which can be used to identify people or equipment
The data from these sensors is combined and processed by the AMR’s onboard computer to create a comprehensive understanding of the environment.
Decision-making
Autonomous mobile robots also use artificial intelligence and machine learning algorithms to make decisions about their movements. These algorithms enable them to:
- Plan paths: AMRs can plan paths that are the most efficient and safest, taking into account obstacles, traffic, and other factors
- Avoid obstacles: AMRs can detect and avoid obstacles in real time, preventing collisions and ensuring safe navigation
- Adapt to changing environments: AMRs can learn from their experiences and adapt to changes in their surroundings, such as new obstacles or changes in traffic patterns
- Collaborate with humans: AMRs can interact with humans, sharing information and coordinating tasks
Movement
Autonomous mobile robots use a variety of motors and actuators to move around their environment. These motors and actuators control the wheels, arms, or other appendages of the AMR, allowing it to move in a controlled and precise manner.
Communication
Autonomous mobile robots can communicate with other robots, computers, and humans using a variety of methods, such as Wi-Fi, Bluetooth, and radio. This communication enables them to share information, coordinate tasks, and receive instructions.
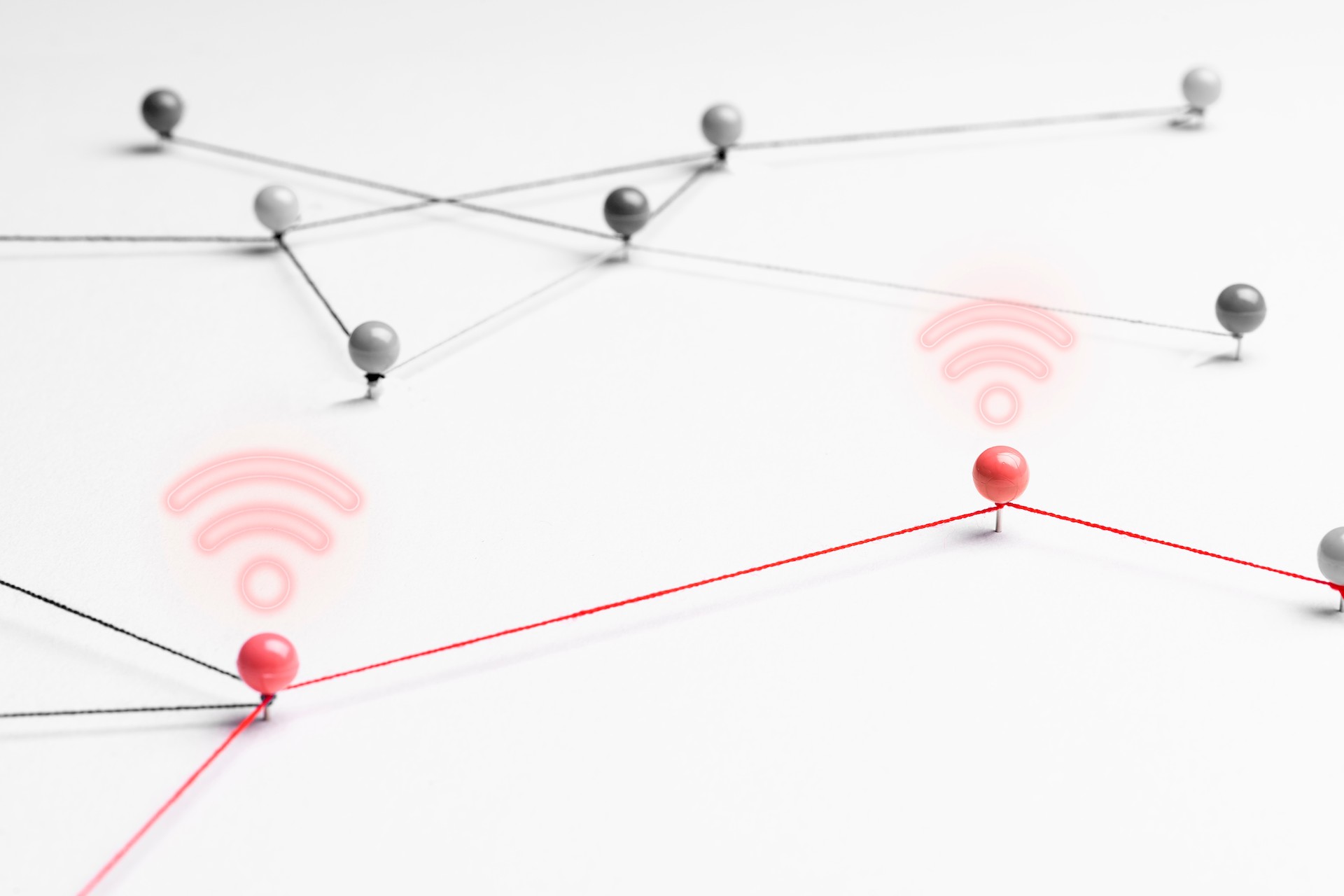
Safety
Autonomous mobile robotss are designed with safety in mind. They are equipped with sensors and software that enable them to detect and avoid hazards, such as people, obstacles, and hazardous materials. Autonomous mobile robots also have safety features that prevent them from moving if they are in a dangerous situation.
What are the differences between AMRs and AGVs?
Autonomous mobile robots (AMRs) and automated guided vehicles (AGVs) are both types of mobile robots used for material handling tasks. However, there are some key differences between the two.
Navigation
The most significant difference between AMRs and AGVs lies in their navigation capabilities. AGVs follow predefined paths, typically marked on the floor with wires or magnetic tape. They rely on sensors to detect and avoid obstacles, but they cannot adapt to changing environments or replan their routes.
AMRs, on the other hand, are truly autonomous, meaning they can navigate their surroundings without predefined paths. They use sensors, artificial intelligence, and machine learning to create maps of their environment and make decisions about their movements in real time. This allows them to adapt to dynamic environments, avoid obstacles, and even collaborate with humans.
Flexibility
AGVs are generally less flexible than AMRs due to their reliance on predefined paths. Changing the layout of a warehouse or factory where AGVs are deployed can be time-consuming and expensive.
AMRs, on the other hand, can be easily adapted to changing environments, similar to swarm robotics. They can learn new paths and adjust to changes in their surroundings without the need for infrastructure modifications. This makes them a more flexible and versatile solution for material handling tasks.
Applications
AGVs are typically used in applications where there is a high degree of predictability and where the environment is relatively static. For example, they are commonly used in manufacturing facilities to transport goods and materials between workstations.
AMRs are better suited for applications where there is a need for flexibility and adaptability. They are increasingly being used in warehouses and distribution centers to automate picking and packing tasks, as well as in healthcare settings to deliver medications and supplies to patients.
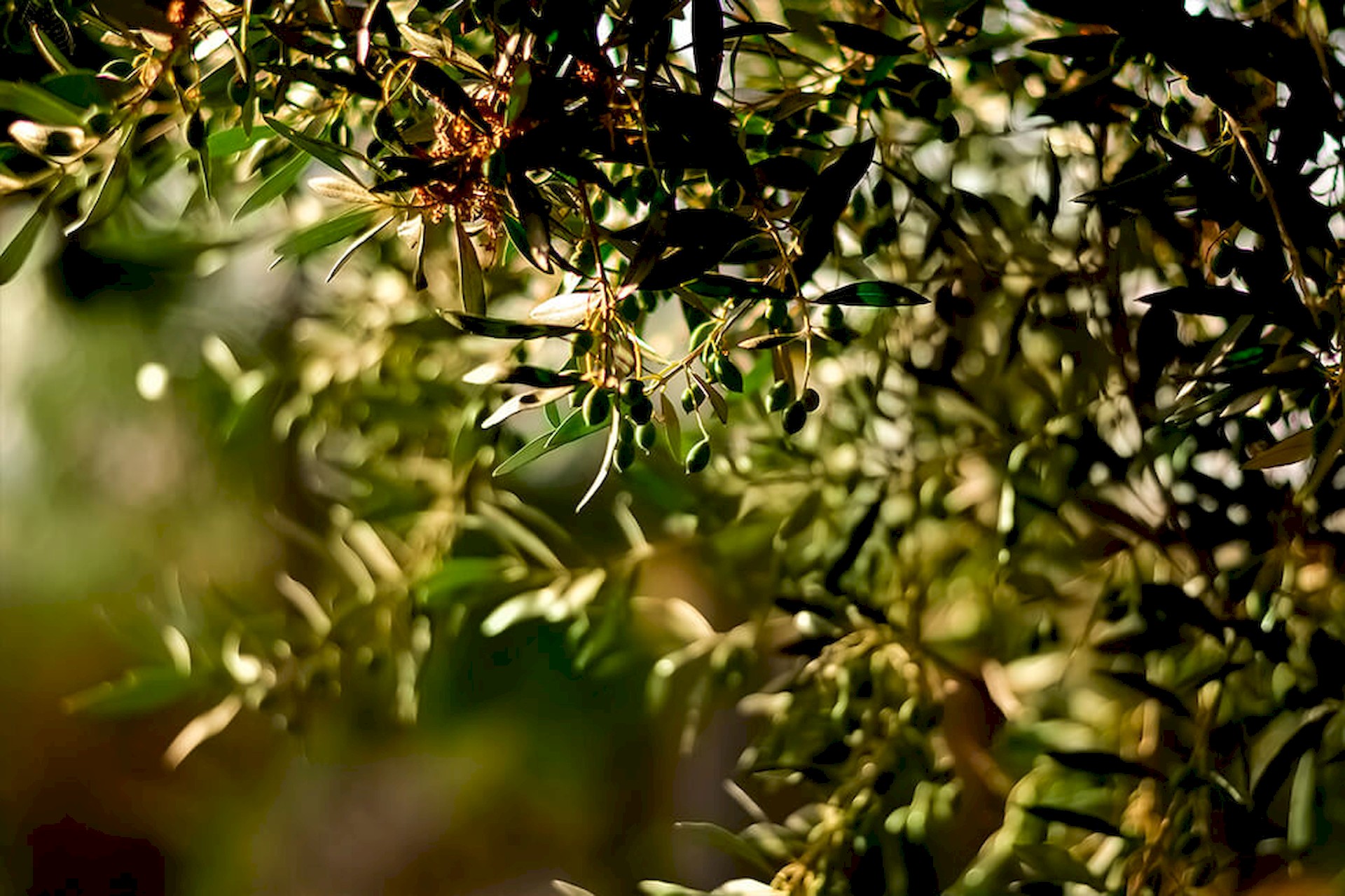
Cost
AGVs are generally less expensive to purchase and maintain than AMRs. However, the cost of installing and maintaining infrastructure for AGVs can offset some of these savings. Additionally, the inflexibility of AGVs can lead to additional costs if the layout of an environment changes.
AMRs are typically more expensive upfront, but their flexibility and adaptability can lead to long-term savings. They can also be integrated into existing infrastructure, reducing the need for additional costs.
Here is a table below that summarizes the key differences between autonomous mobile robots and automated guided vehicles.
Feature | AGVs | AMRs |
Navigation | Predefined paths | Autonomous navigation |
Flexibility | Less flexible | More flexible |
Applications | Predictable, static environments | Dynamic, changing environments |
Cost | Lower upfront cost | Higher upfront cost |
Infrastructure | Requires infrastructure | No infrastructure required |
AMRs are rapidly evolving with the technology, and their capabilities are constantly expanding. As artificial intelligence and machine learning continue to develop, probably sooner than we think thanks to NVIDIA’s H200, autonomous mobile robots will become even more sophisticated and capable. They will be able to perform more complex tasks, collaborate more seamlessly with humans, and operate in even more challenging environments. Autonomous mobile robots have the potential to rewrite the rules of work and life and find new ways to interact with the world around us.
Featured image credit: Emre Çıtak/Bing Image Creator.
- SEO Powered Content & PR Distribution. Get Amplified Today.
- PlatoData.Network Vertical Generative Ai. Empower Yourself. Access Here.
- PlatoAiStream. Web3 Intelligence. Knowledge Amplified. Access Here.
- PlatoESG. Carbon, CleanTech, Energy, Environment, Solar, Waste Management. Access Here.
- PlatoHealth. Biotech and Clinical Trials Intelligence. Access Here.
- Source: https://dataconomy.com/2023/11/15/what-are-autonomous-mobile-robots-uses/