Introduction
Throughout history, humans have had an insatiable desire to understand the world around them, including the stars. The science of rocketry has been developing for centuries, even predating our current era. Today’s rockets are the result of numerous experiments and the combination of many different areas of engineering. Few things can withstand the extreme conditions that rockets must endure, including the intense loads during launch and drastic temperature changes caused by cryogenic components and combustion chambers. Successful launches depend heavily on well-informed design decisions. The complexity and interdependence of the systems that must work together seamlessly in rocket design are unparalleled by any other engineering discipline. It is no coincidence that they say “rocket science” when it comes to something incredibly complex. Figure 1 displays numerous advanced rocketry systems over several decades.
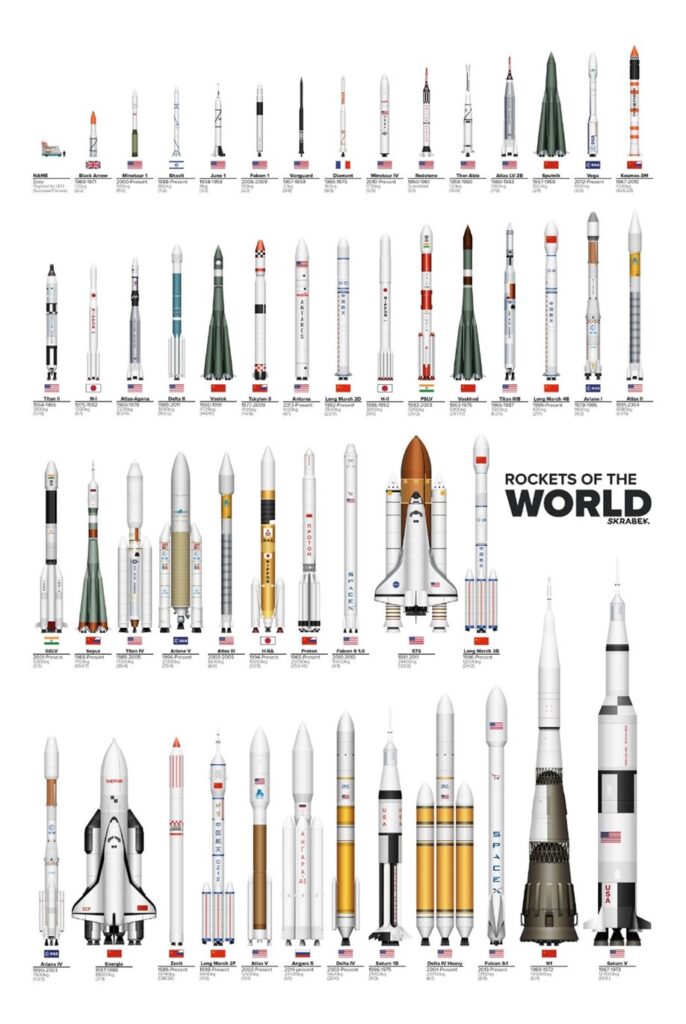
Rocketry’s origins trace back to ancient China, where the first rockets were created around 100 AD. These early rockets were used during religious celebrations and produced colorful sparks, smoke, and explosions using gunpowder and bamboo tubes that were closed on one end. The first recorded use of rockets in warfare occurred during the Battle of Kai-Keng in 1232, where the Chinese used a primitive solid-fuel rocket to repel the Mongols. The rocket consisted of a closed tube filled with gunpowder attached to a long stick. Ignition of the gunpowder increased pressure inside the empty tube, and the hot gas and smoke had to escape through the open end. By the law of conservation of momentum, this creates thrust to propel the rocket towards the closed end of the tube, with the long rod as a primitive control system.

From the 16th century onwards, several notable individuals made significant contributions to the advancement of rocket science. Kazimir Semenovich, Isaac Newton, Konstantin Tsiolkovsky, and Robert G. Goddard were among them. Goddard proposed using a supersonic Laval nozzle to increase the speed at which hot gases are ejected, a crucial innovation in rocket design. Overall, these inventors shaped solid rockets into their present form.
Consider the most commonly used rocket schemes
Solid-propellant thruster scheme
Solid rockets have undergone a significant evolution since their invention in the 13th century, but there have been some key developments that have shaped solid rockets as they are found today. Here are some of the most significant factors that have contributed to the development of modern solid rockets:
- Improved propellant formulations: Over time, scientists and engineers have developed more efficient and powerful propellant formulations for solid rockets. Early propellants were simple mixtures of saltpeter and sulfur, but modern propellants are much more sophisticated and can produce much higher thrust.
- Advances in manufacturing: Solid rocket technology has benefited from manufacturing processes that have made it possible to produce more consistent and reliable rocket motors. One significant development was the invention of casting techniques that allowed the propellant to be molded into the desired shape. Another breakthrough was automated machinery to produce rocket motors more quickly and efficiently.
The latest examples of developed Solid-Propellant thrusters are the SLS (NASA) boosters and the first three VEGA (ESA) boosters.

Advantages:
- Cone nozzles are typically used instead of profiled nozzles
- High reliability. There are practically no moving parts in these engines
- Cheap
Disadvantages:
- Increased storage requirements to avoid changes (pores, cracks) in the structure of an already-filled propellant
- Lower ISP compared to liquid-propellant engines
Additional features when working with solid fuels include the presence of the k-phase (solidification of solid particles on the nozzle) and the “blurring” of the tapering nozzle and critical section by solid fuel particles. These can lead to a change in the cut profile, a change in the combustion area, and uneven combustion, resulting in changes and inconsistencies in the main parameters.
Pressure-fed thruster scheme
In a pressure-fed thruster, the propellant tanks are pressurized with an inert gas, such as helium, which forces the propellant out of the tanks and into the engine. The fuels are then mixed and burned in the combustion chamber, producing high-pressure exhaust gases that exit through the nozzle, providing thrust.
The pressure-fed thruster cycle has several advantages over other rocket engine cycles, including its simplicity and reliability. As there are no pumps or turbines to drive, pressure-fed thrusters are less complex and require less maintenance than other rocket engines. They are also less prone to mechanical failures and can operate for extended periods without refueling.
However, pressure-fed thrusters also have some disadvantages. They typically have lower thrust-to-weight ratios than other rocket engines, which limits their use in applications that require high acceleration or thrust. They also have limited flexibility in adjusting the thrust level during flight, as the tank pressure determines the propellant flow rate.
Despite their limitations, pressure-fed thrusters are commonly used in small satellites and other space applications that require low to moderate thrust levels. They are also used as auxiliary engines on larger rockets, providing small bursts of thrust for course corrections and other maneuvers.

Advantages:
- Simple
- Reliability
- No turbopumps
- High specific impulse
Disadvantages:
- Tank pressure limits combustion chamber pressure and thrust
- Heavy tanks and associated pressurization hardware
Gas-generator thruster scheme
The gas generator cycle is one of the oldest and most studied rocket engine cycles still in use today. It is a type of staged combustion cycle in which fuel and oxidizer are burned in separate combustion chambers. In the gas generator cycle, a small amount of fuel and oxidizer is burned in a preburner, which drives a turbine to pump more fuel and oxidizer into the main combustion chamber. The fuel and oxidizer are then burned in the main combustion chamber, producing high-pressure exhaust gases that exit through the nozzle to provide thrust.
The gas generator cycle has several advantages, including high efficiency and thrust-to-weight ratio. However, it also has some disadvantages, such as a lower specific impulse (ISP) than other liquid-propellant engines.
The gas generator cycle was first used on the V-2 rocket by Germany during World War II. The V-2 rocket used a gas generator cycle, which was a simple and reliable engine design at the time. The engine used a liquid fuel mixture of ethanol and water and a liquid oxidizer (liquid oxygen) that were fed into the engine through separate pumps. Germany chose the gas generator cycle for the V-2 rocket due to its simplicity and reliability, which were critical factors for the wartime application of the rocket.
Despite its limitations, the V-2 rocket was a significant milestone in the development of rocket technology and paved the way for future space exploration. Some of the latest examples of developed open cycle liquid rocket engines are the Merlin engine on the Falcon 9 rocket by SpaceX and the Vulkan engine on the Ariane 5 rocket by ESA

Advantages:
- Simple
- Low dry mass
- ISP higher than solid-propellant fuel
- Allows for high-power turbopumps for high thrust
Disadvantages:
- Lower ISP than other liquid-propellant engines
Staged combustion thruster scheme
Staged combustion is an advanced rocket engine cycle used in some of the most powerful rocket engines, such as the RD-180 (Russian) and the Raptor (SpaceX). Unlike other rocket engine cycles, which typically use separate exhaust systems for fuel and oxidizer, the staged combustion cycle uses the remaining fuel-rich exhaust gases to drive the turbine that powers the propellant pumps. This allows for more efficient use of the propellants, as the remaining exhaust gases burn entirely, and the energy is not wasted.
The staged combustion cycle has several advantages over other rocket engine cycles, including higher specific impulse and efficiency, resulting in a greater thrust-to-weight ratio. It also allows for more flexibility in adjusting the thrust level during flight, as modifying the preburner and main combustion chamber pressures can alter the propellant flow rate.
However, the staged combustion cycle also has some disadvantages. It is a complex and challenging cycle to design and operate, requiring high-precision and high-temperature materials to withstand the harsh combustion environment. It also demands a high level of control and monitoring, as any malfunction or imbalance in the preburners or main combustion chamber can lead to catastrophic failure.

Advantages:
- High specific impulse
- High combustion chamber pressures allow for high thrust
- Allows for high-power turbopumps for high thrust
Disadvantages:
- Complexity is greatly increased, including the number of details and mass (especially for full-flow)
In a full-flow staged combustion thruster scheme, the fuel and oxidizer are initially fed into separate preburners, where they are partially burned to generate a high-pressure and high-temperature gas mixture. This gas mixture is then fed into the main combustion chamber, which is fully burned to produce high-pressure exhaust gases that exit through the nozzle, providing thrust.

Advantages:
- The highest specific impulse is achieved because there is no energy loss for gasifying components in the combustion chamber
Disadvantages:
- Development complexity and cost
- Lack of prototypes
Cycle with electric pumps thruster scheme
The electric pump-fed cycle is a newer type of rocket engine cycle that is gaining popularity due to its simplicity and reliability. In this cycle, an electric motor drives the fuel and oxidizer pumps, eliminating the need for a turbine. The fuel and oxidizer are then burned in a combustion chamber, producing exhaust gases that exit through the nozzle to provide thrust.
The electric pump-fed cycle has several advantages, including simplicity, reliability, and the ability to use a wide range of fuels. However, it also has some disadvantages, such as lower efficiency, high battery weight, and lower thrust-to-weight ratio than the gas generator cycle.

Advantages:
- High specific impulse
- Fairly low complexity
- Reliability
- No turbopumps
Disadvantages:
- High battery weight
Conclusions
Rocket scientists aim to reduce costs and the time between launches. Light and medium-lift launchers are the most common and easiest to launch, but they have a high cost per kilogram of payload. These rockets use simple and proven solutions like the gas generating cycle and LOX + RP-1 propellants, but there is also interest in exploring new solutions like hybrid air-jet rocket cycles and hybrid propulsion schemes.
Super-heavy launch vehicles have the lowest launch price in low Earth orbit, but they are expensive, complex, and have a long waiting window. They require advanced designs, such as engines with the highest specific impulse.
Upper-stage engines should be as simple as possible, using designs like pressurized or monopropellant rockets, and self-igniting propellant components, to reduce weight and cost.
In all other cases, rocket scientists choose the simplest design with a minimum number of components and sufficient energy intensity to ensure reliability and reduce complexity and cost.
Looking to learn more about the tools used in this blog? Check out AxSTREAM System Simulation to solve your most complex rocket engine challenges or request a trial!
References:
- The History of Rocket Science https://aerospaceengineeringblog.com/history-of-rocket-science/
- SEO Powered Content & PR Distribution. Get Amplified Today.
- Platoblockchain. Web3 Metaverse Intelligence. Knowledge Amplified. Access Here.
- Source: https://blog.softinway.com/a-comparison-of-different-rocket-engine-cycles-throughout-the-years/