Different requirements
In manufacturing businesses, production run lengths have become shorter, due in part to the real or imagined need for product extensions that address narrow customer and consumer needs. There is less of high volume Make to Stock (MTS) and more of High Mix, Low Volume (HMLV) under descriptors of Make to Order (MTO) and Assemble to Order (ATO). This can influence the planning at contract manufacturers, outsourced production, suppliers and 3PLs.
In any situation where a business offers more items, or Stock Keeping Units (SKUs) for a given output, there will be more competition for operating resources, and therefore variability in resource utilisation. To achieve the most effective operations requires a focus on capacity – of facilities, machine, people and input supplies.
The need is to differentiate Planning and Scheduling between the horizon for decisions, management’s time availability and the volume of data and information to be analysed and considered. Planning is tactical and mainly concerned with people and their willingness to collaborate. This is to enable a common understanding about the future, and to identify and agree on outcomes. However, Scheduling is operational, being concerned with any resource that can affect productive output (i.e., machines and their fixtures, people and supplies) and therefore must have a detailed schedule of use.
One Plan
Although having different time and data needs, the Planning and Scheduling process must be contained within the ‘One Plan’ approach, shown in the diagram.
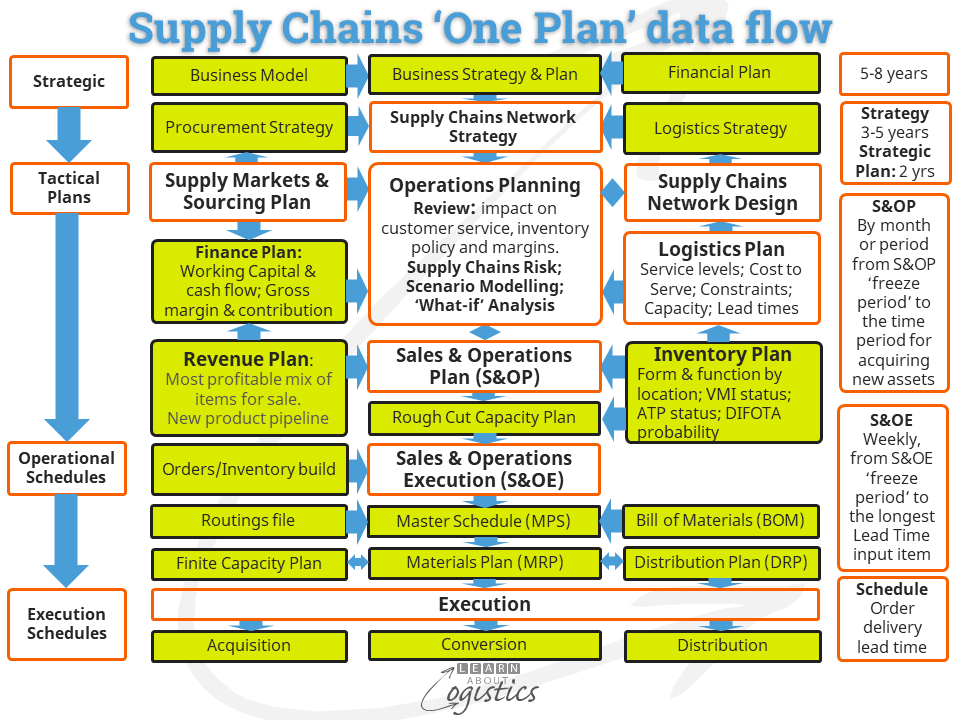
Although the base data remains the same, the level of granularity changes at each stage of the process flow:
- The Sales & Operations Planning (S&OP) process horizon commences at month three (or period three, each of 4 weeks). Month/period one and two (the ‘freeze’ period) have already been scheduled within the Sales & Operations Execution (S&OE) process. S&OP is therefore undertaken at a consolidated level of detail as discussed in the previous blogpost. Here, the measure of capacity used is the ‘demonstrated’ capacity; that is the current performance of a machine or production line, accounting for unplanned events, such as breakdowns and interruptions. Also, include the time for changeover between production runs. For example, on a plastics production line, the changeover time from black to white is much longer (due to a washout) than from white to black. In food, the changeover of chocolate from milk to dark is shorter than from dark to milk.
- Within Sales & Operations Execution (S&OE), the horizon for Operational schedules is from the current scheduling ‘freeze’ period (which could be the next two weeks) out to the longest lead time of purchased materials and intermediate items. Operations schedules require detailed inputs to be effective – of the task, resources (machines and people) required and the time to complete the tasks. Also, at this level is the potential for connection of equipment for online data collection via SCADA (supervisory control and data acquisition) systems, through the Industrial Internet of Things (IIoT). Equipment performance can be profiled and analysed for scheduled maintenance to be incorporated into the Operational schedule; also as input to ‘digital twin’ simulation of Operations.
- For Execution schedules, the horizon is the lead time for current customer orders. To account for interruptions and delays in production, yet still meet the Operations schedule, the Execution schedule can have some orders starting early, and others starting late late, to align with the availability of resources.
- The Operational and Execution schedules must be linked to the Available to Promise (ATP) system, so there is ‘one source of truth’ concerning current availability of SKUs for use in online ordering and by Customer Service personnel.
Link between Planning and Scheduling
The link between Planning and Schedules is the Bill of Materials. This is constructed for each product or Stock Keeping Unit (SKU) and defines (on a quantity per basis) the materials and intermediate goods used The routing plus set-up and operating times are defined based on data from the Routings file. Fields in the BoM identify the SKUs ‘family’ (or supply chain), to be used in the S&OP process. Also, a capability to convert the SKU measurement (weight, volume, packaging etc.) into the standard unit of measure used for S&OP (tonnes, litres, standard shipper etc.).
This capability enables the Plan from S&OP (can be the Rough Cut Capacity Plan (RCCP) within the ERP system) to be entered into the S&OE Master Schedule as a forecast for the applicable future periods. To do this, the S&OP over the planning horizon is disaggregated into individual SKUs, based on historical sales percentages.
As the BoM requires the ‘quantity per’ for each supplied material and intermediate goods, the S&OP can plan material requirements for input to the Procurement Category Management process. In the S&OE process, the Materials Requirements Plan provides a schedule for acquiring contracted inputs.
Scheduling Capacity
The challenge occurs when when scheduling capacity. The traditional approach (and software construction) is based on the concept of infinite capacity used for the RCCP. When scheduling operations, the software assumes there is infinite capacity and only indicates when capacity is exceeded, relying on people to make the necessary adjustments. This enables a relatively easy implementation and use, which is acceptable for RCCP due to the long horizon used in S&OP.
However, scheduling operations requires finite scheduling that knows the capacity limitations. To do this requires (at least) the updating and input of: operational sequencing rules (e.g. the colour sequence to use or transfer batch size to the next operation); alternative routing; machine throughput; machine set-up times; customer priority rules.
The output from a finite capacity scheduling routine will be a sequence of activities and tasks at each work centre throughout the facility. The Operations Schedule for the current period remains firm; however, the Execution Schedule (which commences as a copy of the Operations Schedule) can be adjusted to comply with current conditions, with some work commencing early and some late, but the Schedule output is the goal.
A make or assemble to order operations model requires the ability to accurately schedule a variety of products in relatively small order quantities. But additional variety products required with quicker response times can increase costs. It is therefore not advisable to use infinite scheduling routine that may be incorporated in an ERP system. Instead, the requirement is for a finite scheduling application that can interface to the current ERP system.
- SEO Powered Content & PR Distribution. Get Amplified Today.
- PlatoData.Network Vertical Generative Ai. Empower Yourself. Access Here.
- PlatoAiStream. Web3 Intelligence. Knowledge Amplified. Access Here.
- PlatoESG. Carbon, CleanTech, Energy, Environment, Solar, Waste Management. Access Here.
- PlatoHealth. Biotech and Clinical Trials Intelligence. Access Here.
- Source: https://www.learnaboutlogistics.com/the-scheduling-part-of-operations-planning-and-scheduling/#utm_source=rss&utm_medium=rss&utm_campaign=the-scheduling-part-of-operations-planning-and-scheduling