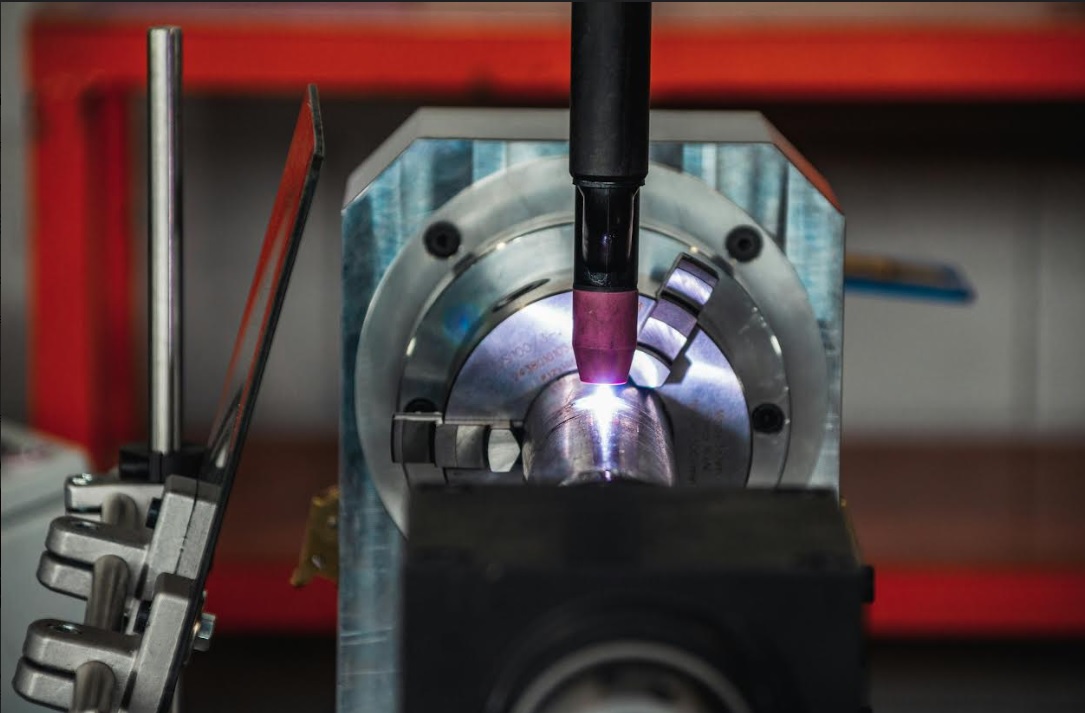
The journey of welding technology has been remarkable, evolving from basic forge welding to today’s sophisticated electric arc and gas techniques. This evolution has consistently expanded the possibilities in manufacturing and construction. The recent shift toward integrating AI into these processes marks a significant milestone, transitioning from manual and semi-automated methods to fully automated, AI-enhanced systems.
These advanced systems offer unparalleled precision, real-time adjustments and predictive maintenance capabilities.
“Integrating AI boosts efficiency and quality and heralds a new era of innovation, blending cutting-edge technology with traditional craftsmanship.”
The Rise of AI in Welding
AI introduces levels of precision, efficiency and safety previously unattainable. AI-driven systems are adept at automating complex welding tasks that require high accuracy, adapting in real time to material variances and welding conditions to ensure optimal quality. These systems can predict and mitigate potential hazards, significantly improving health and safety conditions for operators by reducing exposure to harmful fumes and intense heat.
Further, AI enhances productivity by streamlining processes, reducing waste and ensuring consistent output, delivering greater customer value. This transformative impact of AI in welding is not just about doing the job faster — it’s about doing it smarter, safer and with superior results. This innovation marks a new chapter in industrial manufacturing where technology elevates the process and the product.
Benefits of AI-Enhanced Robotic Welding
Incorporating AI into welding processes brings unmatched performance benefits, including increased efficiency, improved weld quality and significant waste reduction.
Harnessing the power of AI lets these systems analyze vast data sets to fine-tune welding parameters in real time, adapting to different materials and varying conditions with unparalleled precision. This ability to optimize settings on the fly ensures consistent, high-quality welds and minimizes material overuse and scrap, contributing to more sustainable manufacturing practices.
Additionally, AI-driven welding equipment operates at peak efficiency, reducing the time and resources required for each task. This combination of enhanced quality, efficiency and sustainability sets a new benchmark in welding performance, offering substantial advantages to industries seeking to stay at the forefront of innovation and productivity.
Addressing the Skills Gap
AI-enhanced systems bridge the skills gap in the welding industry by executing complex welds with minimal human intervention, alleviating the demand for highly skilled welders. These systems work alongside human operators, enhancing product quality and production speed through seamless collaboration. Cobots perform precise and repetitive tasks, allowing people to focus on the welding process’s more intricate and quality-critical aspects.
“Additionally, AI trains and assists human welders, offering simulations and real-time feedback that sharpen their skills and boost productivity.”
This symbiotic relationship between AI technology and human expertise elevates welding projects’ overall quality and efficiency. It empowers the workforce, making advanced techniques more accessible and less reliant on extensive manual experience.
Challenges and Solutions
Integrating AI into welding faces several challenges, notably the high initial costs of purchasing and setting up advanced equipment. Likewise, the need for specialized training for operators to use these technologies effectively hinders this approach.
These hurdles can deter small to medium enterprises from adopting AI solutions. However, the industry is actively addressing these challenges by developing more user-friendly AI systems that require less technical expertise to operate, lowering the barrier to entry.
Additionally, there’s a growing emphasis on comprehensive training programs tailored for welders, focusing on equipping them with the skills needed to work alongside AI technologies and cobots. These initiatives aim to democratize access to AI in welding, ensuring businesses of all sizes can leverage these advancements to enhance their competitiveness and efficiency.
Future Trends in AI-Enhanced Welding
AI in welding has combined with other cutting-edge technologies, like the IoT and 3D printing. This paves the way for a fully automated manufacturing process. This synergy enables real-time monitoring and control of welding operations. It’s enhanced by the precision of 3D-printed parts tailored for specific tasks, streamlining production lines for efficiency and minimal human error.
Such advancements can propel the global robotic welding market, which can grow to over $9 billion by 2028. This growth underscores the increasing reliance on robotic welding to meet the demands of modern manufacturing, highlighting a future where technology drives productivity and innovation to new heights.
Staying Ahead With AI Welding Innovations
Staying informed about the latest advancements in AI welding technology is crucial for anyone looking to understand the future of manufacturing. These innovations promise to enhance efficiency and quality across the board and signify a significant leap toward fully automated and optimized production processes.
Also Read Is the Release of ChatGPT AI Going to Affect the Education Industry?
- SEO Powered Content & PR Distribution. Get Amplified Today.
- PlatoData.Network Vertical Generative Ai. Empower Yourself. Access Here.
- PlatoAiStream. Web3 Intelligence. Knowledge Amplified. Access Here.
- PlatoESG. Carbon, CleanTech, Energy, Environment, Solar, Waste Management. Access Here.
- PlatoHealth. Biotech and Clinical Trials Intelligence. Access Here.
- Source: https://www.aiiottalk.com/future-of-welding-ai-enhanced-robotic-systems/