Oct 28, 2023 |
|
(Nanowerk Spotlight) From the vivid blues and greens of peacock feathers to the shimmering reds of ruby crystals, structural color in nature provides some of the most dazzling displays that delight our eyes. Unlike pigments that absorb certain wavelengths to produce color, structural color arises from the physical interaction of light with nanoscale features in a material. This makes such “photonic” materials more sustainable, resistant to bleaching and allows for dynamic tunability. However, shaping them into complex 3D geometries has remained an enduring challenge.
|
3D printing has been shown to be an effective approach for manufacturing photonic crystals – materials with periodic nanostructures that control light propagation by creating photonic bandgaps. But photonic crystals rely on long-range order and have been limited to simpler shapes using printing.
|
Now, researchers at ETH Zurich have harnessed the technique of digital light processing (DLP) 3D printing to create structurally colored photonic colloidal glasses with complex geometries and tailored color properties.
|
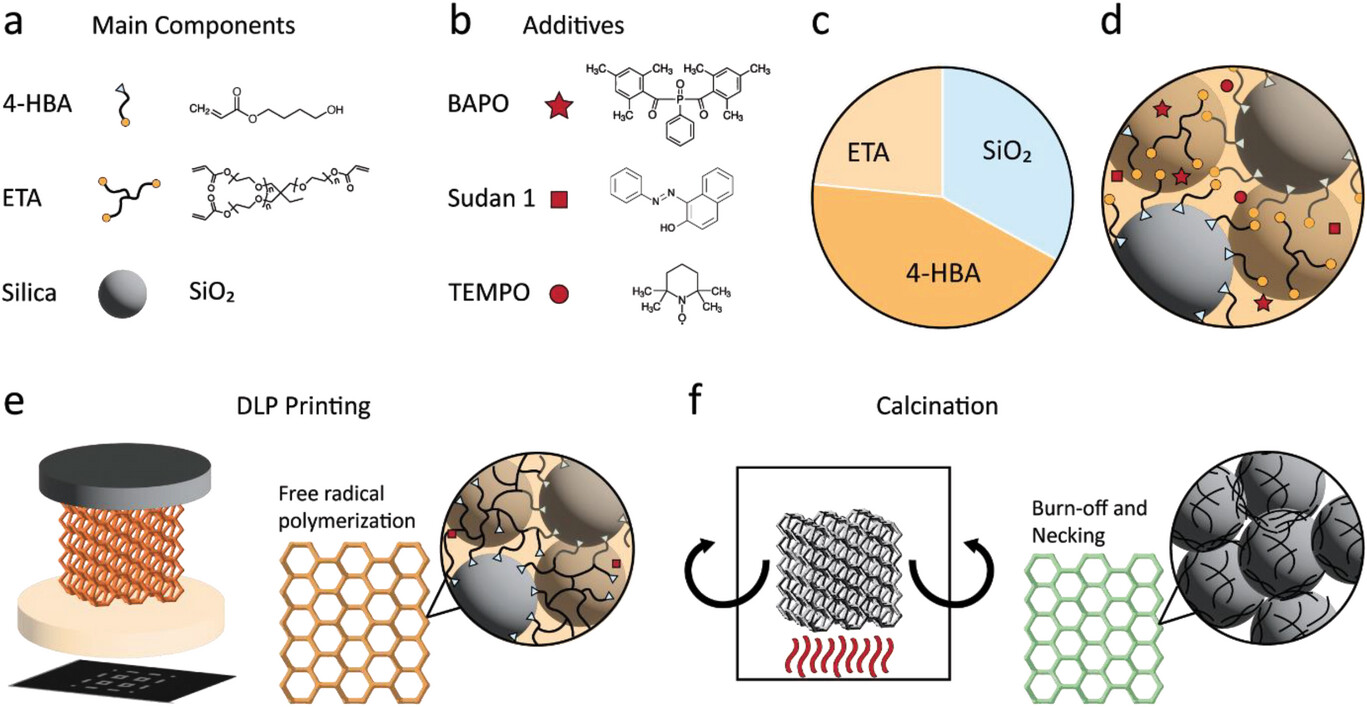 |
Schematics of the workflow used for the fabrication of complex-shaped photonic colloidal glasses by DLP 3D printing. a–d) Typical resin formulation comprising silica colloidal particles suspended in a photoreactive monomer mixture. e,f) Cartoons of the working principle of the DLP printing process highlighting the microstructures of complex-shaped 3D objects after the printing of the resin and calcination of the printed parts. (Reprinted with permission by Wiley-VCH Verlag)
|
Their work, published in Advanced Materials (“Light-Based 3D Printing of Complex-Shaped Photonic Colloidal Glasses”), demonstrates how combining rationally designed materials and additive manufacturing can expand the design space for photonic devices.
|
The researchers focused on photonic glasses – a class of disordered photonic materials containing size-controlled nanoparticles that interact with light to produce sustainable, non-iridescent structural color that can be tuned across the visible spectrum. The combination of short-range order and long-range disorder leads to vivid, non-iridescent structural color.
|
To create such materials, the team started with a customized resin containing crosslinkable monomers, photoinitiators and silica nanoparticles. Using a commercial DLP 3D printer, they solidified this liquid resin into 3D objects by curing it layer-by-layer using light projection.
|
The key step came next: high temperature heating at 400 C transformed the printed polymer matrix into a glassy material with desired structural order. The team demonstrated they could control the final material’s color by tuning the size of silica nanoparticles to 200, 350 and 300 nm to get blue, green or red shades respectively.
|
Detailed spectroscopy and electron microscopy analysis revealed that the observed color stemmed from selective light scattering by the locally ordered but globally disordered nanoparticles. Comparing the peak reflected wavelengths to theoretical predictions confirmed this mechanism.
|
One issue the team had to carefully control was avoiding multiple scattering that would destroy color purity. They achieved this by calcination protocols that left behind an ideal amount of carbon residue – enough to limit penetration depth but not too much to allow surface reflection.
|
Armed with the ability to prescribe color and shape, the researchers printed complex centimeter-scale 3D architectures. Multimaterial lattices with precisely defined regions of red, green and blue were demonstrated. By spatially modulating scaffold geometries, graded color variations were encoded into 3D octet trusses during the same pyrolysis step. To highlight the shaping freedom of 3D printing, the team also fabricated photonic replicas of cultural artifacts.
|
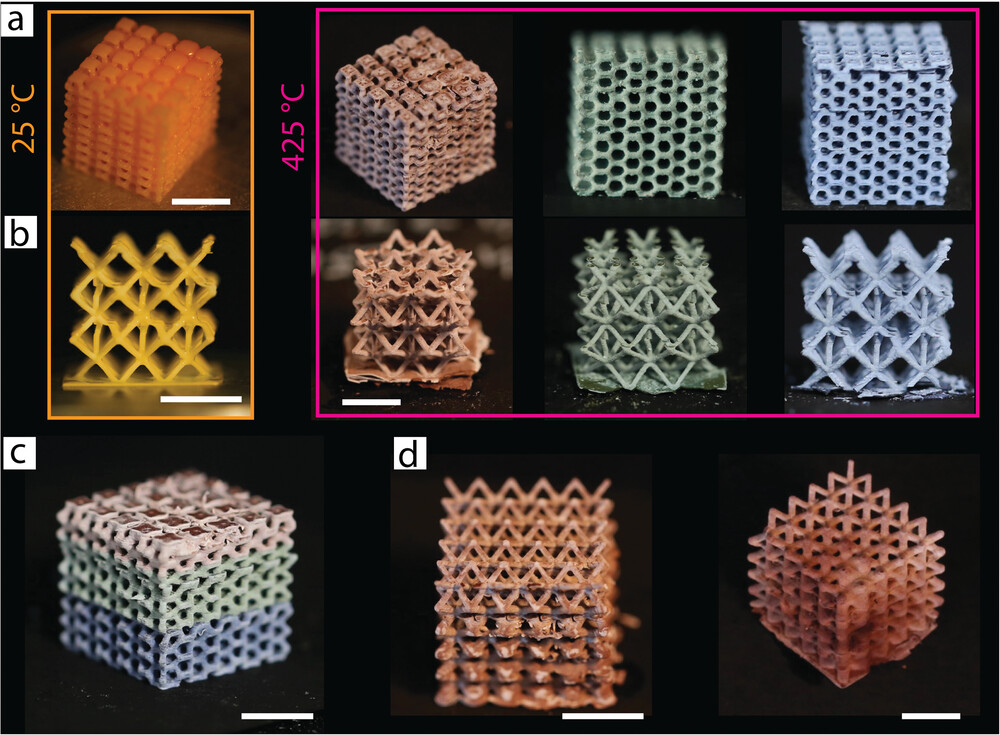 |
Complex-shaped photonic colloidal glasses manufactured by DLP-printing. a,b) Examples of honeycomb and octet-truss lattices featuring distinct structural colors depending on the particle size used in the initial resin. The images show photographs of the 3D lattices before (left) and after (right) calcination for resins with monodisperse silica particles with average sizes of 300, 250, and 200 nm (from left to right). c) Multimaterial, structurally colored lattice with honeycomb architecture obtained by DLP printing and calcination of resins containing 200, 250, and 300 nm silica particles. d) Octet-truss lattices designed to display a color gradient in specific directions by tuning the cell sizes and thus the local permeability of the structure to oxygen during calcination. Scale bars: 5 mm. (Reprinted with permission by Wiley-VCH Verlag)
|
The results establish DLP-based additive manufacturing as a promising route for designing complex-shaped photonic components. Access to intricate non-iridescent structural color can benefit applications in colorimetric sensing, anti-counterfeiting, displays and camouflage. From a materials perspective, the calcination-based technique offers sustainable color formation simply using silica and carbon.
|
Extending the current visible range to UV or infrared could enable additional applications in spectroscopy, imaging and human-machine interactions. By bringing together rational design and advanced manufacturing, this study highlights the future potential of additive production for structurally complex photonic devices.
|
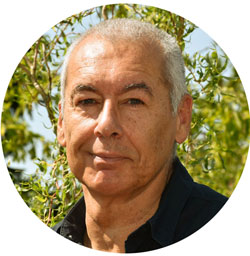
By
Michael
Berger
– Michael is author of three books by the Royal Society of Chemistry: Nano-Society: Pushing the Boundaries of Technology, Nanotechnology: The Future is Tiny, and Nanoengineering: The Skills and Tools Making Technology Invisible Copyright ©
Nanowerk LLC
|
|
- SEO Powered Content & PR Distribution. Get Amplified Today.
- PlatoData.Network Vertical Generative Ai. Empower Yourself. Access Here.
- PlatoAiStream. Web3 Intelligence. Knowledge Amplified. Access Here.
- PlatoESG. Carbon, CleanTech, Energy, Environment, Solar, Waste Management. Access Here.
- PlatoHealth. Biotech and Clinical Trials Intelligence. Access Here.
- Source: https://www.nanowerk.com/spotlight/spotid=63956.php