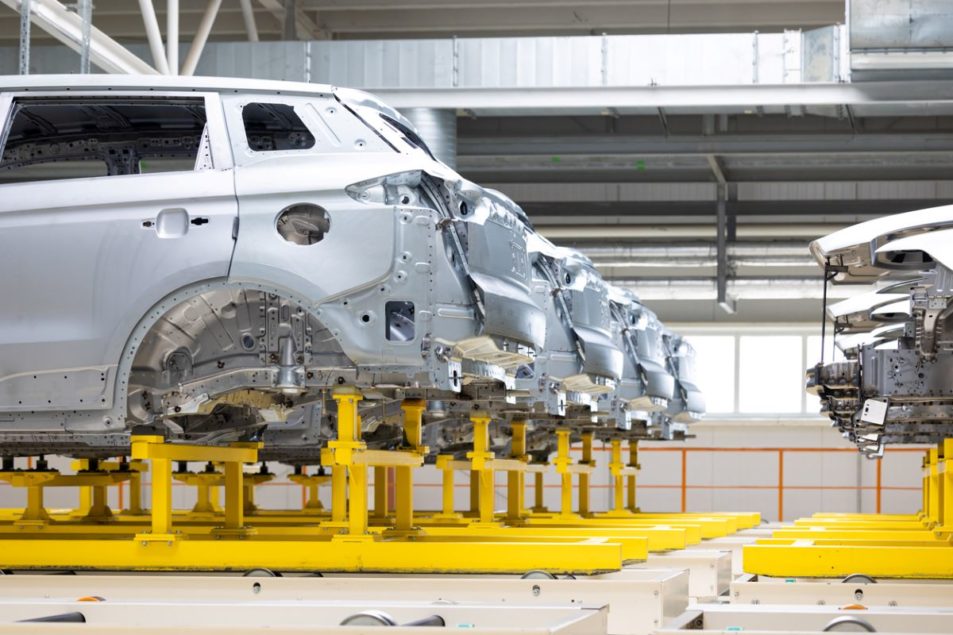
There are signs of recovery in the embattled automotive supply chain, but true relief is still a few years away.
Carmakers were among the hardest hit by disruptions in supplies of key raw materials and components over the last three years, even if the crisis was in part a result of their own actions.
Or inactions, to be more precise, in the form of cancelled orders for microprocessors in response to a slump in auto sales in the early months of the COVID-19 pandemic. When demand for product began unexpectedly to surge later in the year, it was too late to call back those orders. Makers of video games and other types of consumer electronics had already snapped up the capacity left on the table by auto manufacturers, and it would be some time before they would get it back.
The result was a severe shortage of both new and used cars in the marketplace. In response to the dearth of chips, automakers were forced to cut production of new vehicles by an estimated 10.5 million units in 2021, and another 3.6 million in 2022.
Despite a generally pessimistic outlook for the auto industry extending well into 2023, there are some signs of “stabilization” across multiple commodity groups in the industry’s supply chain, says Richard Barnett, chief marketing officer with Supplyframe. He sees slight improvements in supplies of both passive and active microchips, as well as power control systems and other major analog components.
Barnett describes industry’s attempts to cope with the persistent shortages as a game of Whac-a-Mole, whereby manufacturers succeed in obtaining one type of material while suffering a shortfall in another. The problem, he says, lies in an inability to “look under the hood” of their supply chains — in other words, a lack of visibility by original equipment manufacturers of the complete bill of materials. That’s why their outlook for recovery seems so erratic. “The pattern is going to continue to play out into the first half of 2023,” he says.
Automakers managed to lessen some of the pain through forward buying of certain materials, but those actions were offset by their decommitting demand for microchips, and the ripple effect it had throughout the supply chain. What’s more, they were caught short by overreliance on a just-in-time strategy for feeding production lines, which left them without buffer inventory to make up for the halt in supplies triggered by the pandemic.
“Often they would only learn about parts shortages because they weren’t getting shipment confirmations from suppliers — even those that were co-located with manufacturing locations,” Barnett says. “They were getting surprised two to three weeks out, and learning that there was a six-month lead time.”
Over time, the OEMs began reconfiguring their supply strategies, in some cases reaching out to secondary suppliers or buying up as many parts on the open market as possible. But they have continued to suffer disruptions caused by ostensibly minor items over which they lack line of sight — so-called “popcorn parts” like diodes and resistors. Ford Motor Co. warned investors that it would be incurring an extra $1 billion in supply chain costs during the third quarter of this year, and other major automakers are likely to be eating similar costs.
The rise in popularity of electric vehicles has only served to worsen automakers’ plight. Between 1,800 and 2,500 individual electric components go into an internal combustion engine, Barnett says. EVs typically incorporate twice that number. And when such items are buried in subassemblies and originate beyond Tier 1 suppliers, “It’s very easy to have blind spots on, say, 100 ‘non-critical’ components that can still stop production.”
That said, the overall lead time for microprocessors has “improved broadly” in recent months, Barnett says. Where supply gets stuck is components designed for specific vehicle platforms, which are tightly sequenced in limited-volume runs, and are tough to coordinate with suppliers. Moreover, a lot of the new microprocessor capacity set to come on line is concentrating on the “bleeding edge” of technology — the kind of chips that are best suited for high-end electronics and mobile phones, instead of the legacy systems found in most cars.
Real recovery for automotive supply chains is still three to five years down the road, Barnett predicts. And investments in beefing up supply won’t begin to impact production significantly until 2023 at the earliest. Meanwhile, manufacturers will need to continue retooling production lines to accommodate the making of more EVs, which are expected to dominate new-car sales within a matter of years. They will be aided by a push to expand domestic chip production, as well as standardize platform design among multiple vehicle models to reduce sourcing and assembly complexity.
“Every EV program allows OEMs to get their act together around standardization and reuse,” Barnett says. “It allows them to get ahead of the problem by doing more long-term agreements, direct sourcing and collaboration with semiconductor suppliers than ever before.”
- Coinsmart. Europe’s Best Bitcoin and Crypto Exchange.Click Here
- Platoblockchain. Web3 Metaverse Intelligence. Knowledge Amplified. Access Here.
- Source: https://www.supplychainbrain.com/blogs/1-think-tank/post/36131-automotive-supply-chains-are-on-a-long-road-to-recovery