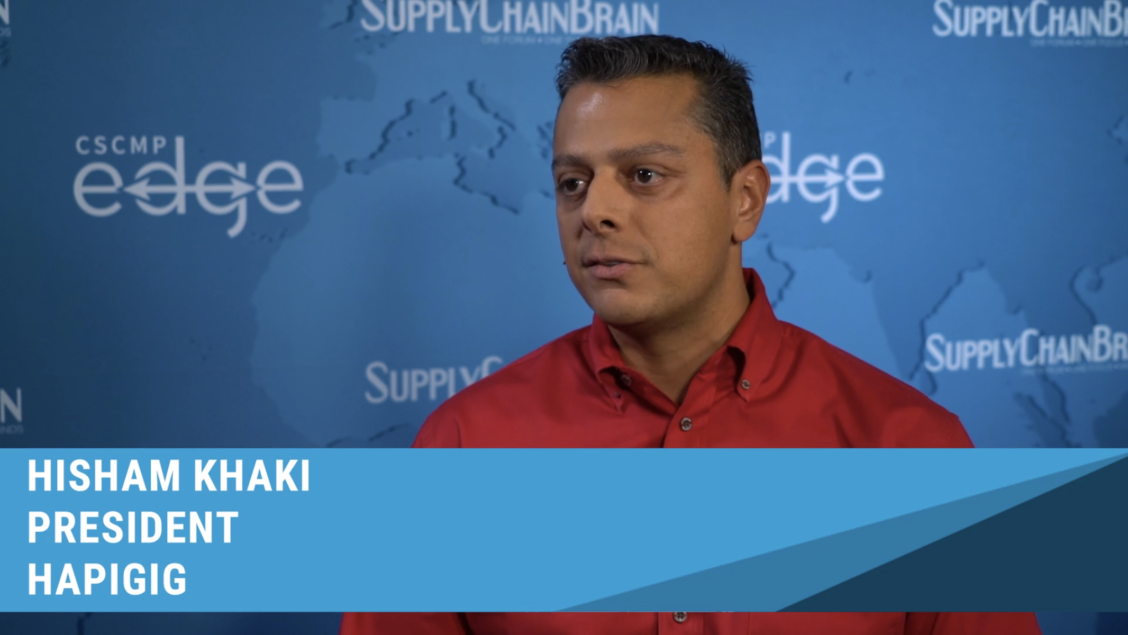
As variability has ramped up in the warehouse, a flexible workforce has become a necessity, says Hisham Khaki, president of HapiGig.
Ten to 15 years ago, variability in the warehouse wasn’t that much of an issue, says Khaki, but that has drastically changed. Whereas before orders were received for shipment in two or three days, now items are picked and loaded for next-day delivery. And the variance in volume can be great. “One day your volume’s 100,000 units. Next day, your volume drops down to 75,000. Next day, 125,000. So variability over the past decade has become more and more of an issue within the warehousing industry.”
The highs and lows cause havoc with labor. “Say that you have a completely static workforce of 75 warehouse workers, and they’re trying to take care of that volume,” says Khaki. That’s going up and down, up and down. That creates a nightmare for many warehouses because you either have too many people or not enough people.” The trick for employers is to match the right number of workers for peaks and lows.
The number of workers needed depends on order volume, of course, but labor management can be difficult, especially if sudden increases result in too few people working 12-hour days, six days a week, Khaki says.
No one wants to be overworked, and today’s warehouse employee desires flexibility in his or schedule. “After pay, the number-two thing that warehouse workers want is flexibility. So, time to take off with their family, and the ability to work more hours when needed, just not the type of schedule that calls for the exact same 40 hours a week.”
Warehouse operators see the demand for schedule flexibility whether employees want simple work, such as “hand” unloading, or jobs handling forklifts, cherry pickers or a variety of trucks.
- SEO Powered Content & PR Distribution. Get Amplified Today.
- Platoblockchain. Web3 Metaverse Intelligence. Knowledge Amplified. Access Here.
- Source: https://www.supplychainbrain.com/articles/35947-watch-for-warehouses-variability-demands-flexibility