Lean manufacturing tends to reduce waste and make the production process more cost-effective and efficient as well. The primary focus is to streamline production operations while enhancing customer experience. To make this possible, lean manufacturing optimises production operations by emphasizing customer needs. Overall, lean manufacturing is about terminating things that do not add value, therefore adhering to delivering the product based on the needs of the customers and fulfilling the expectations, says Ritesh Sutaria, co-founder of Prompt Softech.
Using a low-code platform with manufacturing can support manufacturers in solving several issues. Studies show that production processes in operations only add value 5% of the time, while the rest 95% are usually wasted. Waste in production means any operation that adds no value and is not useful to the customer. This includes transport, inventory, motion, over-processing, defects, waiting, and over-production. Hence, lean manufacturing plays a vital role in production.
Benefits of lean manufacturing
The concept of lean manufacturing was developed by Toyota Production System, one of the most renowned and successful automobile manufacturers. Toyota pioneered these principles, including real-time manufacturing marked by low inventory levels and highly automated functioning supervised by only a set of professionals to control the quality of the product and reduce downtime. Let’s have a look at a few specific benefits of lean manufacturing:
#1: Progress in customer service:
The main objective of lean manufacturing is to add value for the customer. It emphasizes what customers want and when they need it. An enterprise can become successful if its customers are happy and satisfied. As long as a company can fulfill the customers’ needs and demands, they keep returning, and business will thrive without barriers.
#2: Ease of management
One advantage of opting for lean manufacturing is that it decreases the need for human resources. It prioritises achieving more with fewer people. The reduction in the workforce means there will be a need for only a few people available to manage. It implies that a single operator can easily handle different types of equipment. We can say that lean manufacturing is a bottom-up approach where workers can enhance their performance and results.
#3: Modification in quality and decrease in defects
Curbing waste and additional costs enhance the product value along with quality. Any flaws present in the quality manufacturing process can also be eliminated smoothly.
#4: Waste minimisation
One of the important tenets of lean manufacturing is waste reduction. Waste reduction can improve the quality and pace of the production operation whilst adding value for the customer.
#5: Financial savings
The decline in waste and defects fetches high financial advantages for manufacturers. The money saved by adopting lean manufacturing can be used for priority tasks like quality improvement and matching customers’ needs.
#6: Saving supply inventory
Supply inventory during production is saved with better quality materials and the least defects. It means it can save supply materials during the process.
What Is low-code software?

Lean manufacturing targets waste reduction and optimisation of the production process. To successfully implement a lean manufacturing approach, manufacturers must reduce materials usage and production defects.
To achieve this, manufacturers must keep an eye on all aspects of the production process, from the highest scrap production and usage of materials to quality problems, etc.
Manufacturers must use fast and seamless ways for employees to gather data and monitor systems on the production floor or as a part of the quality management process. Traditional paper forms take a lot of time and do not promise accuracy and rich data collection.
The best solution is low code or no code software that allows manufacturers to digitise data collection to track these aspects of the production process closely.
Low code enables employees to develop powerful apps that track manufacturing processes (like inventory, inspections, etc.). It permits manufacturers to embrace lean manufacturing practices at a much lower price without hiring experienced developers.
In case of market changes, citizen developers can smoothly upgrade the software. Manufacturers can develop successful apps that collect data on any mobile device using low code or no code solutions.
Low-Code for lean manufacturing:
Let’s look at some ways through which low code promotes lean manufacturing.
More agility and greater automation:
As mentioned earlier, swift and efficient delivery is one of the main features of lean manufacturing. It concentrates on delivering products to customers promptly without barriers. Using low-code or no-code software, manufacturers can develop mobile-friendly applications almost ten times faster than traditional app development techniques. Low code or no code offers easy and quick changes or updates. It also automates different processes like job assignments, work instructions, user instructions, etc. It channelises the entire production operation, and lets managers stay updated with incoming, completed, and delayed tasks.
Implementing smart factories
Using low-code platforms, manufacturers can get real-time data showing the machine output, providing greater visibility and productivity. The real-time data also helps in pre-empting maintenance needs, which usually demand a large downtime.
Today, the manufacturing sector is evolving at a pace to match the incoming wave of digital information. The manufacturing sector is all set to join Industry 4.0(smart factories), powered by technologies like artificial intelligence, machine learning, advanced analytics, cloud computing, etc.
Low code or no code platforms can support installing smart factories by consolidating data silos by linking data from various systems into a single application. It helps predict real-time demands and improves efficiency by integrating all the systems and processes.
As organisations accumulate real-time signals of all the working processes of the production floor, they can improve the efficiency of the entire process.
Continuous development:
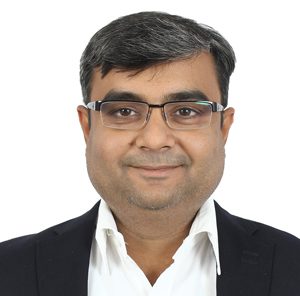
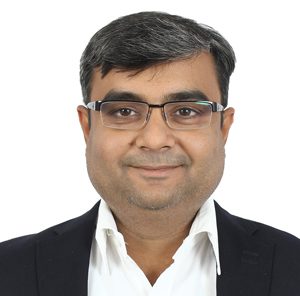
Unorganised production operations can cause chaos on the production floor. As we already know, low-code platforms can assist in developing apps that offer greater visibility to the manufacturer. It empowers manufacturers to calculate the time taken in each process segment and analyse its best practices. Manufacturers can connect the best practices into their operations to guarantee that their employees are working to a minimum working standard.
Low-code apps allow customisation, enabling manufacturers to track workers’ activities, productivity, and location. With such access to multiple data points, managers and workers can work together to achieve optimal performance and productivity.
The low-code approach:
Low-code or no-code assists manufacturers in executing a lean manufacturing approach and advancing towards Industry 4.0 revolution. The main objective is to channel the production process whilst enhancing customer experience.
The author is Ritesh Sutaria, co-founder of Prompt Softech.
Comment on this article below or via Twitter: @IoTNow_OR @jcIoTnow