07 년 2023 월 XNUMX 일 (나노 워크 뉴스) 미국 에너지부 오크리지 국립연구소(Oak Ridge National Laboratory) 연구원들은 NASA와 협력하여 NASA가 로봇 달 탐사선에 사용했던 디자인과 동일한 종류의 바퀴를 3D 프린팅하여 적층 제조를 최종 개척 단계로 끌어올리고 있습니다. 우주 탐사에 필요한 부품. 적층 제조된 바퀴는 NASA가 2024년에 달 남극의 얼음과 기타 잠재적 자원의 지도를 작성하기 위해 보낼 계획인 이동 로봇인 VIPER(Volatiles Investigating Polar Exploration Rover)의 기존 경량 바퀴를 모델로 했습니다. 이번 임무는 달 물의 출처와 분포를 파악하고 달 표면에서 그곳에 사는 사람들을 지원할 만큼 충분한 물을 채취할 수 있는지 확인하는 데 도움을 주기 위한 것입니다.
단 며칠 만에 ORNL 연구원들은 파우더 베드 프린팅을 사용하여 NASA 디자인을 기반으로 한 달 탐사선 바퀴를 만들었습니다. (이미지: Carlos Jones, ORNL) ORNL의 DOE 제조 시연 시설(MDF)에서 인쇄된 프로토타입 휠은 실제로 NASA 달 임무에 사용되지는 않지만 NASA를 위해 제작된 휠과 동일한 설계 사양을 충족하도록 제작되었습니다. 독사 같은 사람. 미래의 달이나 화성 탐사선에 이 기술을 사용하거나 대형 구조 부품과 같은 다른 우주 응용 분야에 이 기술을 고려하기 전에 설계 및 제작 방법을 검증하기 위한 추가 테스트가 계획되어 있습니다.
적층 제조는 에너지 사용, 재료 낭비 및 리드 타임을 줄이는 동시에 설계 복잡성과 재료 특성 맞춤화를 가능하게 합니다. MDF는 이러한 노력의 선두에 서서 청정 에너지, 운송 및 제조 부문의 광범위한 응용 분야에 대해 XNUMX년 넘게 기술을 개발하고 있습니다. MDF 연구원들은 2022년 가을 ORNL에서 로버 휠 프로토타입을 인쇄했습니다. 특수 3D 프린터는 두 개의 조정된 레이저와 회전하는 빌드 플레이트를 사용하여 금속 분말을 선택적으로 녹여 설계된 모양으로 만들었습니다.
일반적인 금속 파우더 베드 시스템은 다음과 같이 단계적으로 작동합니다. 캐비닛 크기의 기계에서는 고정된 플레이트 위에 파우더 층을 긁어냅니다. 그런 다음 플레이트가 약간 낮아지고 프로세스가 반복되기 전에 레이저가 선택적으로 층을 녹입니다. 로버 휠 프로토타입에 사용되는 프린터는 사람이 들어갈 수 있을 만큼 크며 단계가 동시에 연속적으로 발생하면서 큰 물체를 인쇄할 수 있는 능력이 독특하다고 새로운 레이저 분말층 융합 시스템의 MDF 개발을 이끄는 Peter Wang이 말했습니다.
"이는 동일한 양의 레이저 전력으로 생산 속도를 극적으로 증가시킵니다."라고 그는 말하며 증착이 50% 더 빠르게 진행된다고 덧붙였습니다. “우리는 시스템이 할 수 있는 일의 표면만을 긁어보고 있습니다. 저는 이것이 특히 대규모 및 대량 생산에서 레이저 파우더 베드 프린팅의 미래가 될 것이라고 정말로 생각합니다.” Wang과 프로젝트 팀원은 최근 전기 모터와 같은 인쇄 부품 기술의 확장성을 분석한 연구를 발표했습니다.
기계는 독특하지만 프로젝트 성공의 열쇠는 공정 자동화 및 기계 제어에 대한 연구원의 전문 지식이었습니다. 그들은 ORNL에서 개발한 소프트웨어를 사용하여 휠 디자인을 수직 레이어로 "분할"한 다음 두 레이저 간의 작업량 균형을 맞춰 균등하게 인쇄하고 최근 특허 보호를 위해 제출된 계산 기술을 활용하여 높은 생산 속도를 달성했습니다.
시스템에 의해 생산된 첫 번째 부품 중 하나인 프로토타입 휠은 기관 간 협업의 가치를 보여줍니다. ORNL의 로버 휠 프로젝트를 주도한 연구원인 브라이언 깁슨(Brian Gibson)은 “NASA와의 프로젝트는 실제로 기술 발전을 촉진했습니다.”라고 말했습니다.
적층 제조를 통해 돔 모양의 물결 모양 트레드와 같은 미세한 디자인 세부 사항을 프로토타입 달 바퀴에 통합할 수 있습니다. (이미지: Carlos Jones, ORNL) 니켈 기반 합금으로 제작된 프로토타입 휠은 폭이 약 8인치, 직경이 20인치로 금속 파우더 베드 시스템으로 프린팅된 일반 부품보다 훨씬 큽니다. 이를 위해서는 넓은 작업 영역에 걸쳐 작은 기하학적 형상을 인쇄할 수 있는 기능이 필요했습니다. 적층 제조를 통해 추가 비용이나 제조상의 어려움 없이 림 디자인의 복잡성이 더욱 커졌다고 Gibson은 말했습니다.
이에 비해 내년에 달 먼지를 휘젓게 될 XNUMX개의 VIPER 바퀴에는 여러 제조 공정과 조립 단계가 필요했습니다. VIPER의 50피스 휠 림은 360개의 리벳 조인트로 함께 고정됩니다. 임무의 엄격한 요구 사항을 충족하기 위해 제조 공정에는 복잡하고 시간 집약적인 가공이 필요했습니다.
NASA 테스트를 통해 3D 프린팅된 프로토타입이 기존 방식으로 제작된 바퀴만큼 견고하다는 것이 입증된다면 미래의 로버는 대신 ORNL이 제조하는 데 40시간이 소요되는 단일 프린팅된 휠 림을 사용할 수 있습니다. 프로젝트를 통해 ORNL과 NASA 엔지니어들은 휠의 강성을 높이기 위해 각진 측벽, 돔형 모양 및 물결 모양 트레드와 같은 정밀한 디자인 기능을 프린팅하는 방법도 연구했습니다. 이러한 특성은 전통적인 제조 방법을 사용하는 현재 VIPER 휠 디자인에 통합하기 어렵습니다. 더 복잡한 스포크 패턴과 휠에 대한 스포크 잠금 기능을 활성화했음에도 불구하고 3D 프린팅은 휠 설계 비용을 단순화하고 절감했으며 최종 조립을 더 쉽게 만들었습니다.
NASA의 기계 설계 엔지니어이자 휴스턴에 있는 NASA 존슨 우주 센터의 적층 제조 연구소 관리자인 Richard Hagen은 "이러한 휠 기능 중 상당수는 적층 가공으로 무엇을 할 수 있는지 강조하기 위해 추가되었습니다."라고 말했습니다. "기존 툴링이나 전통적으로 가공된 부품으로는 구현하기 어려운 설계 기능을 쉽게 구현할 수 있습니다." 대형 물체를 인쇄하는 ORNL의 능력은 달과 화성 임무 모두를 위해 훨씬 더 큰 로버 휠을 생산할 수 있는 적층 제조 기술의 잠재력을 보여준다고 Hagen은 말했습니다.
문제는 특수 프린터가 특정 재료(이 경우 니켈 기반 합금)로만 제작된다는 점입니다. 따라서 3D 프린팅 휠은 비슷한 두께로 프린팅하면서도 알루미늄 VIPER 휠보다 50% 더 무겁습니다.
NASA는 NASA 존슨 우주 센터의 암석 뜰이나 계약된 테스트 시설의 시뮬레이션된 달 암석과 토양의 거대한 "모래 상자"에서 로버에서 3D 프린팅된 바퀴의 성능을 테스트할 계획입니다. 평가자는 휠의 기동성, 회전 저항, 측면 미끄러짐, 경사 오르기 및 기타 성능 지표를 평가합니다.
Hagen은 적층 제조가 테스트에 대응하여 신속한 설계 업데이트라는 이점을 제공한다고 말했습니다. 또한 약점을 추가하지 않고도 서스펜션 시스템과 같은 더 복잡한 기능을 통합할 수 있습니다.
Hagen은 기관의 Artemis 프로그램의 일환으로 달에 배치된 유인 연구 스테이션에는 행성 외 제조 능력이 필요하다고 말했습니다. “수리를 위해 공간에서 부품을 제작할 수 있다는 것은 중요합니다. 충분한 예비품을 확보할 수 없기 때문입니다.”라고 그는 말했습니다. "인쇄용 분말, 펠렛 또는 필라멘트는 포장하기가 훨씬 쉽고 유연성이 더 높습니다." "적층 제조는 공급원료가 있으면 우주에서든 지구에서든 필요한 교체 부품을 만들 수 있는 유연성을 제공합니다"라고 Gibson은 말했습니다. 이것이 바로 적층 제조가 빠르게 제조되는 툴링부터 조달하기 어려운 주조 및 단조품에 이르기까지 다양한 교체 요구에 대해 상당한 관심을 불러일으킨 이유입니다.

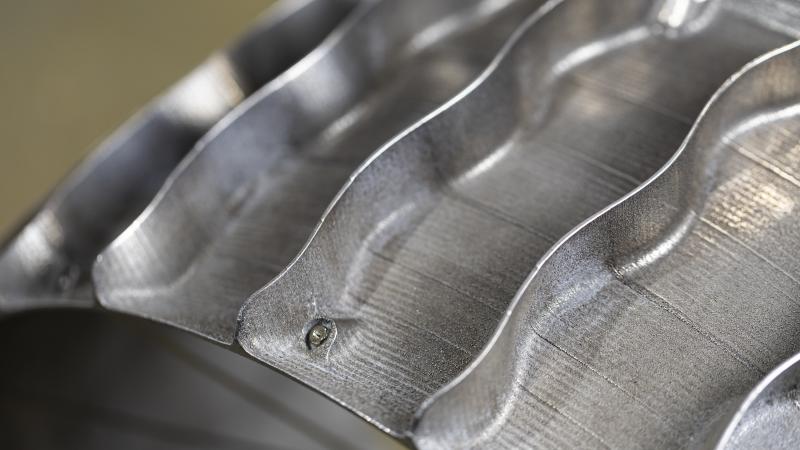
- SEO 기반 콘텐츠 및 PR 배포. 오늘 증폭하십시오.
- PlatoData.Network 수직 생성 Ai. 자신에게 권한을 부여하십시오. 여기에서 액세스하십시오.
- PlatoAiStream. 웹3 인텔리전스. 지식 증폭. 여기에서 액세스하십시오.
- 플라톤ESG. 탄소, 클린테크, 에너지, 환경, 태양광, 폐기물 관리. 여기에서 액세스하십시오.
- PlatoHealth. 생명 공학 및 임상 시험 인텔리전스. 여기에서 액세스하십시오.
- 출처: https://www.nanowerk.com/news2/gadget/newsid=63797.php