
Aby zapobiec potencjalnym awariom, obrażeniom pracowników i stratom w produkcji, coraz więcej firm zapoznaje się ze zdalnym monitorowaniem majątku. Próbują uciekać systemy konserwacji predykcyjnej wychwytywać problemy, zanim wystąpią w produkcji, minimalizując ryzyko niezadowolenia pracowników i klientów oraz zapobiegając utracie pieniędzy.
Na szczęście XXI wiek oferuje nowoczesne i skuteczne rozwiązania z zakresu konserwacji predykcyjnej w produkcji, które można wdrożyć w różnych gałęziach przemysłu.
W ostatnim czasie Prylada przeprowadziła serię wywiadów dotyczących rozwoju klientów, podczas których zwracaliśmy się do ekspertów z branży produkcyjnej. Nasz zespół postawił sobie za cel zebranie cennych informacji nt monitorowanie aktywów i wyzwań związanych z wdrażaniem technologii w branży oraz sposobów, w jaki firmy je rozwiązują.
Podczas rozmów rozmawialiśmy o aktualnej sytuacji na rynku, najbardziej uciążliwych kwestiach, konkurencji oraz rekomendacjach dotyczących efektywnego rozwoju w branży.

Jak zmienił się rynek produkcyjny w ciągu ostatnich 5 lat?
Preferencje konsumentów dotyczące dostosowywania produktów do indywidualnych potrzeb, konkurencyjnych cen i najlepszych ram dostaw stały się głównymi czynnikami skłaniającymi firmy produkcyjne do ponownego przemyślenia swojego podejścia do pracy. Aby nadążać za współczesnymi wymaganiami, muszą zwiększać produktywność poprzez wdrażanie technologii cyfrowych. Technologie te obejmują cyfrowe rozwiązania w zakresie zrównoważonego rozwoju, cyfrowe bliźniaki, autonomiczne roboty mobilne, rzeczywistość rozszerzoną, sztuczną inteligencję i uczenie maszynowe.
"Rzeczywistość w przeszłości była taka, że producenci pracowali w nadgodzinach, wykonywali czynności bardzo ręcznie i nie otrzymywali wsparcia. Po prostu wykonali swoją pracę, a teraz wszystko się zmieniło: od wykonania zadania do miejsca, w którym muszą rozpocząć duże inicjatywy w zakresie transformacji cyfrowej."
- Richard Lebovitz, dyrektor generalny ds LeanDNA
Producenci zaczęli myśleć z następującej perspektywy:
- Musimy być dużo bardziej ze sobą połączeni
- Musimy mieć lepszy wgląd nie tylko w problemy, z którymi się borykamy, ale także w zakresie działań, które musimy podjąć.
Ogólny obraz zmienił się z dotychczasowej pracy na transformację cyfrową, w której priorytetem są działania. Ponadto pandemia Covid-19 uwydatniła znaczenie silnych i elastycznych sieci dostaw. Doprowadziły do znacznych strat wynikających z nieprzewidzianych konsekwencji pandemii firmy przemysłowe do ponownego rozważenia swoich obecnych strategii biznesowych. W rezultacie dążyno do optymalizacji istniejących procesów i zmniejszenia ich uzależnienia od czynników zewnętrznych, zwiększając tym samym odporność na sytuacje siły wyższej.
Nacisk na zrównoważony rozwój staje się siłą napędową szerszego wykorzystania inteligentnych technologii IoT, dzięki czemu przemysł produkcyjny staje się inteligentniejszy, wydajniejszy i zrównoważony, a jednocześnie poprawia dobrostan pracowników. Dzieje się to poprzez automatyzację i transformację cyfrową, a także wykorzystuje analizy predykcyjne w celu generowania lepszych rekomendacji. To z kolei pozwala nam lepiej zrozumieć, jakie są wąskie gardła i wyzwania.
Z drugiej strony proces wdrażania nowych inteligentnych technologii stał się bardziej skomplikowany i czasochłonny. Wyzwania związane z łańcuchem dostaw i niedobory kadrowe skłoniły całą kadrę kierowniczą do głębokiego zaangażowania się w sprawy operacyjne i decyzje na poziomie podstawowym. Skutkowało to większą liczbą interesariuszy, którzy musieli zrozumieć ryzyko, dostosować się do przewidywanych korzyści wartościowych i zrównoważyć te rozważania z innymi inicjatywami firmy.
Szybkie tempo postępu technologicznego w takich obszarach jak automatyzacja, sztuczna inteligencja i Internet rzeczy wymaga od producentów dostosowywania i integrowania nowych technologii w swojej działalności.
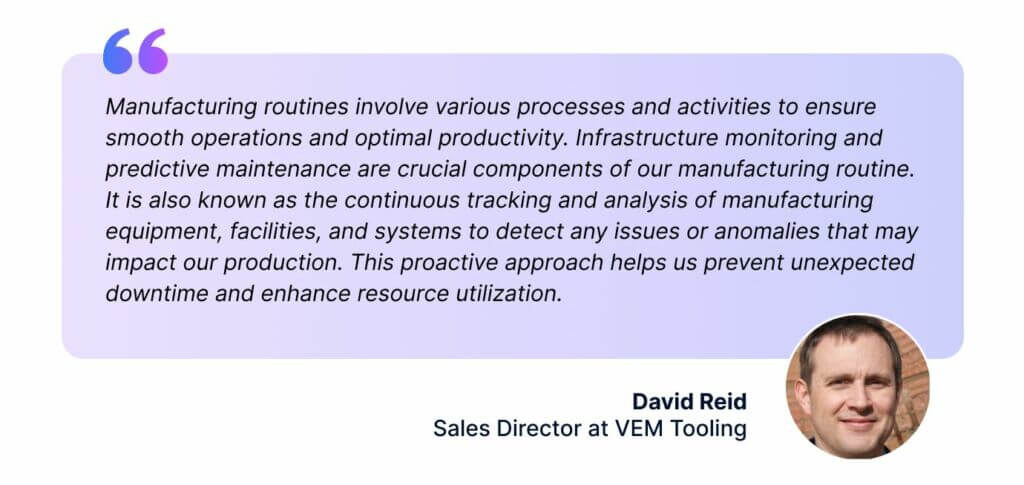
Jednak przejście na nowe technologie monitorowania aktywów może być złożone i kosztowne, wymagać podnoszenia kwalifikacji siły roboczej i zapewniania kompatybilności z istniejącymi systemami.
Zebraliśmy najczęstsze wyzwania i bariery związane z tą transformacją, którymi podzielili się z nami nasi rozmówcy. Na pierwszym miejscu znajdują się punkty, które słyszymy najczęściej. Nie oznacza to koniecznie, że są to choroby najbardziej krytyczne, ale wskazuje na ich rozpowszechnienie. Zacznijmy.
Nieplanowany przestój sprzętu produkcyjnego
Produkcja nowoczesnych urządzeń obejmuje bardzo precyzyjne, złożone procesy i wyrafinowany sprzęt. Nieplanowane przestoje sprzętu produkcyjnego mogą wiązać się z bardzo wysokimi kosztami ze względu na utratę wydajności i stracony czas produkcji. Najnowsze innowacje w zakresie konserwacji predykcyjnej mogą znacznie pomóc w zmniejszeniu utraty produktywności oraz zaoszczędzić wiele wysiłku i czasu.
Jedna z technik z powodzeniem stosowanych w konserwacji predykcyjnej w produkcji wykorzystuje analizę dużych ilości danych dotyczących usterek, konserwacji i danych śledzenia. Aby poprawić jakość wykorzystywanych danych, parametry takie jak proces, znacznik czasu i szczegółowe informacje o komponentach są przypisywane do modeli usterek w celu utworzenia solidnych zbiorów danych. Kilka dużych firm produkujących półprzewodniki zgłosiło stosowanie takich technik w ramach swoich modeli konserwacji predykcyjnej w celu poprawy wydajności.
Wyzwania pozostają nadal, ponieważ wiele złożonych procesów charakteryzuje się częstymi odchyleniami i zmianami. Określone parametry są dostosowywane pomiędzy seriami, aby utrzymać docelowy przebieg procesu. Aby umożliwić odpowiednią kontrolę, można zastosować techniki takie jak wirtualne czujniki monitorujące i rejestrujące konfigurację parametrów w czasie rzeczywistym. Jest to obecnie aktywny obszar badań, a badacze aktywnie badają nowe techniki, w tym sztuczną inteligencję.
Brak narzędzi do gromadzenia danych
Ponieważ ograniczona widoczność zasobów oznacza zwiększone koszty konserwacji i wymiany, wielu producentów już ma trudności z rejestracją podstawowych danych maszyny. Dane te zazwyczaj obejmują temperaturę, wibracje, prędkość i inne wskaźniki wydajności.
Jednak dla wielu firm inwestowanie w narzędzia do gromadzenia danych może być kosztownym przedsięwzięciem. Dlatego wolą pracować z dostępnymi zasobami, które na wiele sposobów mogą utrudniać rozwój.
Producenci chcący wykorzystywać dane w czasie rzeczywistym do monitorowania zasobów potrzebują narzędzia, które może automatycznie łączyć się i zbierać dane z dowolnego źródła. W idealnym przypadku powinien także mieć możliwość normalizowania danych i zarządzania nimi, przeprowadzania analiz i łatwej integracji z aplikacjami innych firm i platformami przetwarzania w chmurze.

Problemy z integracją danych i skalowalnością
Infrastruktura produkcyjna często obejmuje różnorodne systemy, takie jak maszyny, linie produkcyjne i systemy użyteczności publicznej. Systemy te mogły być wdrażane w różnym czasie i przy użyciu różnych technologii. Co więcej, każdy system generuje dane w swoim formacie, co sprawia, że integracja z systemami innych firm jest ogromnym zadaniem. Niespójne formaty, brakujące wartości i niedokładności utrudniają skuteczną integrację.
W miarę ewolucji obiektów i procesów produkcyjnych krajobraz danych rośnie. Systemy muszą być skalowalne, aby pomieścić rosnące ilości danych. Niezbędne jest zapewnienie płynnego i wydajnego przepływu danych w obrębie operacji produkcyjnych bez obciążania infrastruktury monitorowania. Osiągnięcie tego jest możliwe dzięki inwestycjom w nowoczesne narzędzia i stawiając na pierwszym miejscu jakość danych.

Luki w zabezpieczeniach w produkcji
Przemysł produkcyjny stoi w obliczu stale zmieniającego się krajobrazu zagrożeń cybernetycznych, od ataków oprogramowania ransomware po luki w zabezpieczeniach łańcucha dostaw. W kontekście sprzętu komputerowego za główny problem w przypadku półprzewodników uznawano podrabiane produkty o niższej jakości, podczas gdy problemy związane z bezpieczeństwem nie dotyczyły chipów.
Jednak w ciągu ostatnich kilku lat napastnicy znaleźli metody wykorzystania skomplikowanego procesu produkcji półprzewodników. Próbowali manipulować architekturą chipów, wprowadzając złośliwą logikę za pośrednictwem trojanów sprzętowych. Celem atakujących jest wykonanie tych trojanów w celu odmowy usługi (DoS) lub kradzieży danych. W szczególności Syria zgłosiła poważny atak trojana, podczas którego napastnicy umieścili w chipie trojana o nazwie „Kill Switch”, aby wyłączyć syryjski system obrony powietrznej, umożliwiając im wykonanie nalotu.
W ciągu ostatnich kilku lat producenci rozszerzyli zastosowanie koncepcji analizy danych w oparciu o uczenie maszynowe i Internet rzeczy (IoT), aby zapewnić odpowiednią ochronę swojego sprzętu. W przypadku tych technik najpierw inicjują sprzęt dla wszystkich parametrów monitorowania, a następnie stosują algorytmy uczenia maszynowego do tych parametrów, aby przewidzieć klasę parametrów na wyjściu. Jeśli wyniki (wyjście) nie są zgodne z przewidywaniami, producenci mogą zgłosić sprzęt.

Inne przeszkody uniemożliwiające zrównoważoną produkcję
Blokady w łańcuchu dostaw
W przeszłości producenci borykali się z wieloma trudnościami, a prognozy na rok 2024 wskazują na więcej takich problemów. W miarę jak handel światowy staje się coraz bardziej złożony, producenci muszą przygotować się na nieoczekiwane lub nagłe przerwy w swoich sieciach dostaw.
Według niektórych naszych rozmówców, przerwy w łańcuchach dostaw nadal będą jedną z najważniejszych trudności, przed którymi stanie branża w dającej się przewidzieć przyszłości. Obecnie zapasy są na najniższym poziomie od dziesięcioleci, co wskazuje, że niektórych produktów nie można obecnie wytwarzać. Poważny niedobór półprzewodników z Tajwanu, Chin i innych spółek offshore zmusił do zamknięcia niektórych zakładów produkcyjnych branży motoryzacyjnej. Krajowa produkcja również boryka się z trudnościami.
Inflacja
W 2023 r. inflacja była bliska dwucyfrowej wartości ze względu na rosnący popyt i niewystarczającą podaż we wszystkich głównych gospodarkach. W przyszłym roku ceny kluczowych surowców produkcyjnych, takich jak aluminium, ropa i stal, wzrosną jeszcze bardziej, zwiększając presję na firmy, które już próbują obniżać koszty bez utraty jakości.
Lokalizowanie zasobów i inwestycji w celu automatyzacji monitorowania aktywów w czasie inflacji jest trudne. Producenci nie mogą jednak ignorować potencjału, jaki wnosi to dla branży. Może pomóc zredukować błędy ręczne i przyspieszyć zadania nawet 10-krotnie.
Aby sprostać temu wyzwaniu, branża musi przeznaczyć budżet na automatyzację i wprowadzić więcej technologii AI w celu kontroli i automatyzacji zadań w czasie rzeczywistym. Pomoże to nie tylko zaoszczędzić koszty, ale także poprawi wydajność i zmniejszy ilość odpadów.
Wyzwania związane z wdrażaniem technologii cyfrowych
Procesy produkcyjne opierają się na ciągłych, rutynowych harmonogramach i zadaniach realizowanych przez setki dostawców i pracowników w wielu lokalizacjach, a których celem jest produkcja dóbr konsumpcyjnych. To sprawia, że przedsiębiorstwom wyjątkowo trudno jest monitorować bieżące procedury i identyfikować obszary wymagające poprawy.
Producenci mogą łatwo prześledzić każdy etap w całym łańcuchu wartości, wdrażając technologie monitorowania oparte na IoT w czasie rzeczywistym. Takie technologie pomogą im lepiej zrozumieć luki w celach zrównoważonego rozwoju i znaleźć rozwiązania poprawiające wydajność, wydajność i zgodność.
Inteligentne monitorowanie zasobów wiąże się zazwyczaj z dwoma wyzwaniami. Pierwsza polega na integracji i modernizacji starszego sprzętu, aby był kompatybilny z nową technologią, umożliwiając pełne wykorzystanie potencjału Przemysłu 4.0. Drugi zakłada przekwalifikowanie personelu w celu zapewnienia, że będzie on mógł skutecznie monitorować, wykorzystywać i czerpać korzyści z nowego systemu monitorowania.
Mniejsi producenci często uważają, że początkowa inwestycja w nową technologię jest zniechęcająca. Należy jednak pamiętać, że zarówno transformacja cyfrowa, jak i transformacja pracowników to procesy stopniowe. Zmiany te nie pojawiają się z dnia na dzień.
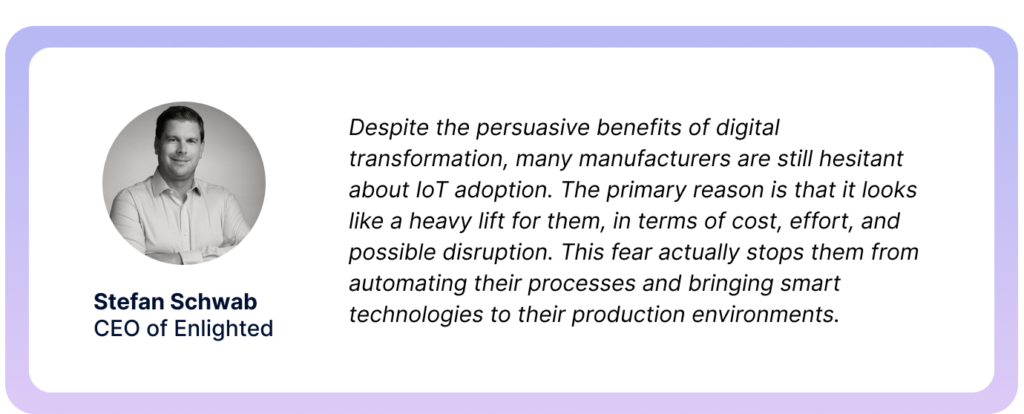
Owijanie w górę
Przemysł produkcyjny już odczuwa skutki automatyzacji i robotyki, takiej jak sztuczna inteligencja, Internet rzeczy, czujniki, roboty na podłodze i szersze wykorzystanie zrobotyzowanej automatyzacji procesów. Rosnące zapotrzebowanie na wdrażanie technologii cyfrowych oraz korzyści, jakie mogą z nich uzyskać firmy produkcyjne, napędzają rozwój cyfryzacji.
W ramach ciągłych wysiłków, aby sprostać wyzwaniom stojącym przed współczesną branżą, producenci wdrażają rozwiązania oparte na IoT w celu inteligentnego monitorowania zasobów. Jednak wybór technologii i możliwości jej wdrożenia zależy jeszcze od możliwości i potrzeb biznesowych.
Nieplanowane przestoje maszyn przemysłowych, problemy z gromadzeniem danych, luki w zabezpieczeniach i ograniczenia skalowalności to wyzwania, które są najważniejsze w środowisku produkcyjnym i którym można sprostać za pomocą technologii monitorowania opartych na IoT. Technologie takie zapewniają producentom szczegółowe, kontekstowe dane w całym łańcuchu dostaw, dzięki czemu mogą szybko zlokalizować problemy i podjąć działania.
Co więcej, mogą również przewidzieć potencjalne problemy, zanim one wystąpią, unikając wycofania produktów i innych znaczących zagrożeń dla środowiska. Z biegiem czasu technologie monitorowania umożliwią użytkownikom śledzenie postępów w realizacji celów zrównoważonego rozwoju i zapewnią zgodność z przepisami branżowymi.
Chcielibyśmy podziękować wszystkim, którzy wzięli udział w naszym wywiadzie dotyczącym rozwoju klienta:
- Vatsal Shah, dyrektor generalny Lakmus
- Stefan Schwab, dyrektor generalny Oświecony
- Tom Richter, globalny dyrektor pionów produkcji dyskretnej i procesowej w branży cyfrowej w firmie Nokia
- Nils Arnold, dyrektor generalny Wstęp
- Duncan Kerr, były dyrektor generalny Aeristech
- Richard Lebovitz, dyrektor generalny ds LeanDNA
- Gulroz Singh, architekt bezpieczeństwa SoC w Półprzewodniki NXP
- Donnie Rand, koordynator ds. marketingu w firmie Amerykańskie Stowarzyszenie Operatorów Właścicieli, LLC
- David Reid, dyrektor sprzedaży w Oprzyrządowanie VEM
- Derrick Hathaway, dyrektor sprzedaży w Medycyna VEM
- Harman Singh, dyrektor ds Cyfera
- Doug Lawson, dyrektor generalny Myśl IQ
- Oraz inni profesjonaliści z branży, których komentarze zostały uwzględnione w tym artykule
- Dystrybucja treści i PR oparta na SEO. Uzyskaj wzmocnienie już dziś.
- PlatoData.Network Pionowe generatywne AI. Wzmocnij się. Dostęp tutaj.
- PlatoAiStream. Inteligencja Web3. Wiedza wzmocniona. Dostęp tutaj.
- PlatonESG. Węgiel Czysta technologia, Energia, Środowisko, Słoneczny, Gospodarowanie odpadami. Dostęp tutaj.
- Platon Zdrowie. Inteligencja w zakresie biotechnologii i badań klinicznych. Dostęp tutaj.
- Źródło: https://www.iotforall.com/experts-discuss-predictive-maintenance-and-innovation-in-manufacturing