Requisiti diversi
Nelle aziende manifatturiere, i tempi di produzione sono diventati più brevi, in parte a causa della necessità reale o immaginaria di estensioni di prodotto che rispondano alle esigenze ristrette dei clienti e dei consumatori. Sotto i descrittori Make to Order (MTO) e Assemble to Order (ATO) sono presenti meno prodotti ad alto volume Make to Stock (MTS) e più prodotti ad alto mix, basso volume (HMLV). Ciò può influenzare la pianificazione presso produttori a contratto, produzione esternalizzata, fornitori e 3PL.
In qualsiasi situazione in cui un'azienda offre più articoli, o unità di stock Keeping (SKU) per un dato output, ci sarà maggiore concorrenza per le risorse operative e quindi variabilità nell'utilizzo delle risorse. Per ottenere le operazioni più efficaci è necessario concentrarsi sulla capacità: di strutture, macchine, persone e forniture di input.
L'esigenza è quella di differenziare la Pianificazione e la Schedulazione tra l'orizzonte delle decisioni, la disponibilità di tempo del management e il volume di dati e informazioni da analizzare e considerare. La pianificazione è tattica e riguarda principalmente le persone e la loro volontà di collaborare. Questo per consentire una comprensione comune del futuro e per identificare e concordare i risultati. Tuttavia, la pianificazione è operativa, poiché riguarda qualsiasi risorsa che può influenzare l'output produttivo (ad esempio, macchine e relativi impianti, persone e forniture) e pertanto deve avere un programma di utilizzo dettagliato.
Un piano
Pur avendo esigenze di tempo e dati diverse, il processo di pianificazione e programmazione deve essere contenuto nell'approccio "Un piano", mostrato nel diagramma.
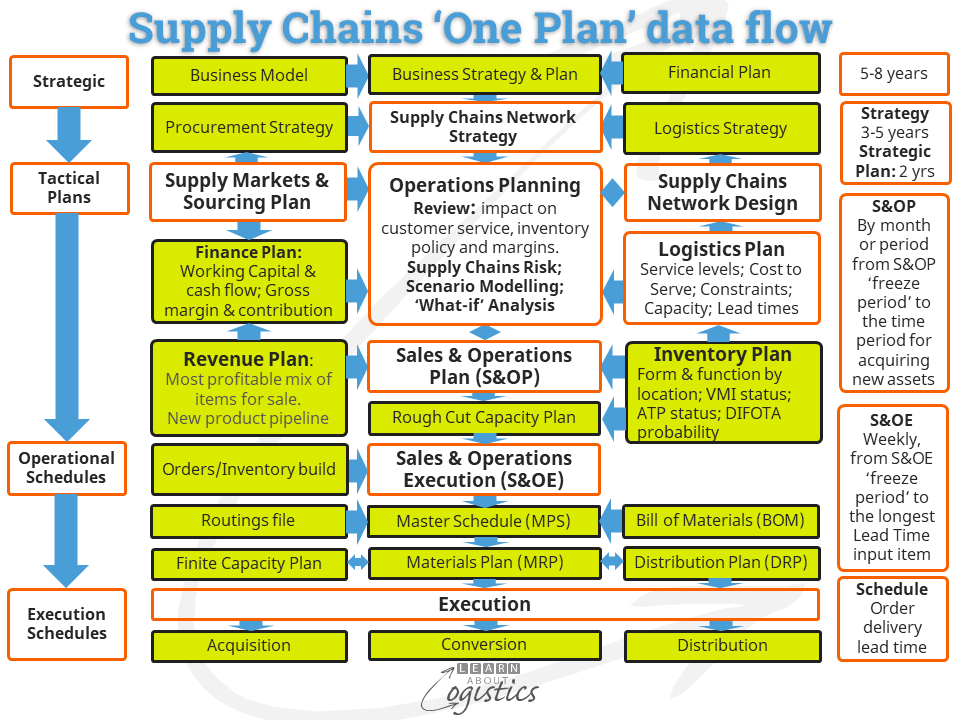
Sebbene i dati di base rimangano gli stessi, il livello di granularità cambia in ogni fase del flusso del processo:
- L'orizzonte del processo Sales & Operations Planning (S&OP) inizia al terzo mese (o periodo tre, ciascuno di 4 settimane). Il mese/periodo uno e due (il periodo di "blocco") sono già stati pianificati all'interno del processo di esecuzione delle vendite e delle operazioni (S&OE). L'S&OP viene quindi intrapreso a un livello di dettaglio consolidato come discusso nel post precedente. Qui, la misura della capacità utilizzata è il 'dimostrato' capacità; ovvero le prestazioni attuali di una macchina o di una linea di produzione, tenendo conto di eventi non pianificati, come guasti e interruzioni. Inoltre, includere il tempo per il passaggio tra i cicli di produzione. Ad esempio, su una linea di produzione di plastica, il tempo di passaggio dal nero al bianco è molto più lungo (a causa di un dilavamento) che dal bianco al nero. Negli alimenti il passaggio del cioccolato dal latte al fondente è più breve che dal fondente al latte.
- All'interno di Sales & Operations Execution (S&OE), l'orizzonte per le pianificazioni operative va dall'attuale periodo di "blocco" della programmazione (che potrebbe essere le prossime due settimane) fino al lead time più lungo dei materiali acquistati e degli articoli intermedi. Per essere efficaci, i programmi delle operazioni richiedono input dettagliati: l'attività, le risorse (macchine e persone) necessarie e il tempo per completare le attività. A questo livello si colloca anche il potenziale per la connessione di apparecchiature per la raccolta dati online tramite sistemi SCADA (controllo di supervisione e acquisizione dati), attraverso l’Industrial Internet of Things (IIoT). Le prestazioni delle apparecchiature possono essere profilate e analizzate per la manutenzione programmata da incorporare nel programma operativo; anche come input per la simulazione "gemello digitale" delle operazioni.
- Per le pianificazioni di esecuzione, l'orizzonte è il lead time per gli ordini cliente correnti. Per tenere conto delle interruzioni e dei ritardi nella produzione e rispettare comunque il programma delle operazioni, il programma di esecuzione può prevedere che alcuni ordini inizino in anticipo e altri inizino in ritardo, per allinearsi alla disponibilità delle risorse.
- I programmi operativi ed di esecuzione devono essere collegati al sistema Available to Promise (ATP), quindi esiste "una fonte di verità" riguardante l'attuale disponibilità degli SKU per l'utilizzo negli ordini online e da parte del personale del servizio clienti.
Collegamento tra pianificazione e schedulazione
Il collegamento tra pianificazione e programmazione è la distinta materiali. Questo viene costruito per ciascun prodotto o unità di stock Keeping (SKU) e definisce (in base alla quantità) i materiali e i beni intermedi utilizzati. Il percorso, i tempi di installazione e di funzionamento sono definiti in base ai dati del file Cicli. I campi nella distinta base identificano la "famiglia" di SKU (o catena di fornitura), da utilizzare nel processo S&OP. Inoltre, la capacità di convertire la misura SKU (peso, volume, imballaggio ecc.) nell'unità di misura standard utilizzata per S&OP (tonnellate, litri, spedizioniere standard ecc.).
Questa funzionalità consente di inserire il Piano di S&OP (può essere il Rough Cut Capability Plan (RCCP) all'interno del sistema ERP) nel Master Schedule di S&OE come previsione per i periodi futuri applicabili. Per fare ciò, l'S&OP nell'orizzonte di pianificazione viene disaggregato in singoli SKU, in base alle percentuali di vendita storiche.
Poiché la distinta base richiede la "quantità per" per ogni materiale fornito e per ogni bene intermedio, S&OP può pianificare i fabbisogni di materiali da inserire nel processo di gestione delle categorie di approvvigionamento. Nel processo S&OE, il piano dei fabbisogni di materiali fornisce un programma per l'acquisizione di input contrattualizzati.
Capacità di pianificazione
La sfida si verifica quando si pianifica la capacità. L'approccio tradizionale (e la costruzione del software) si basa sul concetto di capacità infinita utilizzato per l'RCCP. Quando si pianificano le operazioni, il software presuppone che la capacità sia infinita e indica solo quando la capacità viene superata, affidandosi alle persone per apportare le modifiche necessarie. Ciò consente un’implementazione e un utilizzo relativamente semplici, il che è accettabile per RCCP a causa del lungo orizzonte utilizzato in S&OP.
Tuttavia, le operazioni di pianificazione richiedono una pianificazione finita che conosca i limiti di capacità. Per fare ciò è necessario (almeno) l'aggiornamento e l'inserimento di: regole di sequenziamento operativo (ad esempio la sequenza di colori da utilizzare o trasferire la dimensione del lotto all'operazione successiva); percorso alternativo; produttività della macchina; tempi di attrezzaggio macchina; regole di priorità del cliente.
Il risultato di una routine di pianificazione a capacità finita sarà una sequenza di attività e compiti in ciascun centro di lavoro dell'intera struttura. Resta fermo il Programma delle Operazioni per il periodo in corso; tuttavia, il Programma di esecuzione (che inizia come una copia del Programma delle operazioni) può essere modificato per conformarsi alle condizioni attuali, con alcuni lavori che iniziano in anticipo e altri in ritardo, ma l'obiettivo è l'output della pianificazione.
Un modello operativo di produzione o assemblaggio su ordinazione richiede la capacità di programmare con precisione una varietà di prodotti in quantità di ordine relativamente piccole. Ma la varietà aggiuntiva di prodotti richiesti con tempi di risposta più rapidi può aumentare i costi. Non è quindi consigliabile utilizzare una routine di pianificazione infinita che potrebbe essere incorporata in un sistema ERP. Il requisito è invece quello di un'applicazione di pianificazione finita che possa interfacciarsi con l'attuale sistema ERP.
- Distribuzione di contenuti basati su SEO e PR. Ricevi amplificazione oggi.
- PlatoData.Network Generativo verticale Ai. Potenzia te stesso. Accedi qui.
- PlatoAiStream. Intelligenza Web3. Conoscenza amplificata. Accedi qui.
- PlatoneESG. Carbonio, Tecnologia pulita, Energia, Ambiente, Solare, Gestione dei rifiuti. Accedi qui.
- Platone Salute. Intelligence sulle biotecnologie e sulle sperimentazioni cliniche. Accedi qui.
- Fonte: https://www.learnaboutlogistics.com/the-scheduling-part-of-operations-planning-and-scheduling/#utm_source=rss&utm_medium=rss&utm_campaign=the-scheduling-part-of-operations-planning-and-scheduling